Introduction
Intended Application
The elevator Core drive is intended to control the motor of Counter weighted Traction passenger Elevators, and not intended for hydraulic Elevators.
The elevator Core drive can control Induction or permanent magnet IPM (Internal Permanent Magnet) or SPM (Surface Mounted Permanent Magnet) motor types.
It is the responsibility of the installer to ensure that the equipment or system into which the product is incorporated complies with all relevant legislation and codes of practice which apply in the country of use.
Target Audience
The information detailed within this document is intended for those persons who will mechanically, and electrically install the drive, and those who will program the drive.
Prerequisites
The Installer and user must have Read and understand this manual and other applicable manual in their entirety before proceeding.
This manual is intended as a guide for proper installation. Invertek Drives Ltd cannot assume responsibility for the compliance or the non-compliance to any code, national, local or otherwise, for the proper installation of this drive or associated equipment. A hazard of personal injury and/or equipment damage exists if codes are ignored during installation.
Terminology
The word Drive or Variable Frequency Drive refers to this product, the Optidrive Elevator Core.
IM refers to Induction Motor.
PM refers to permanent magnet motor.
Cyber Security
The overall system designer is responsible for ensuring that there is a maintained secure connection between the drive and any network that could be prone to cyber-attack, furthermore the overall system designer is responsible for applying appropriate measures such as firewalls, data encryption etc..
Invertek Drives Ltd cannot be held responsible for any loss or damages regarding a Cyber Security breach.
About the Product
The drive is intended to control the motor of Counter weighted Traction passenger Elevators, and not intended for hydraulic Elevators.The elevator Core drive can control Induction or permanent magnet IPM (Internal Permanent Magnet) or SPM (Surface Mounted Permanent Magnet) motor types.
The drives rating label carries a part number which details the rating and specification of the drive, the rating label can be found on the side of the drive enclosure as shown below
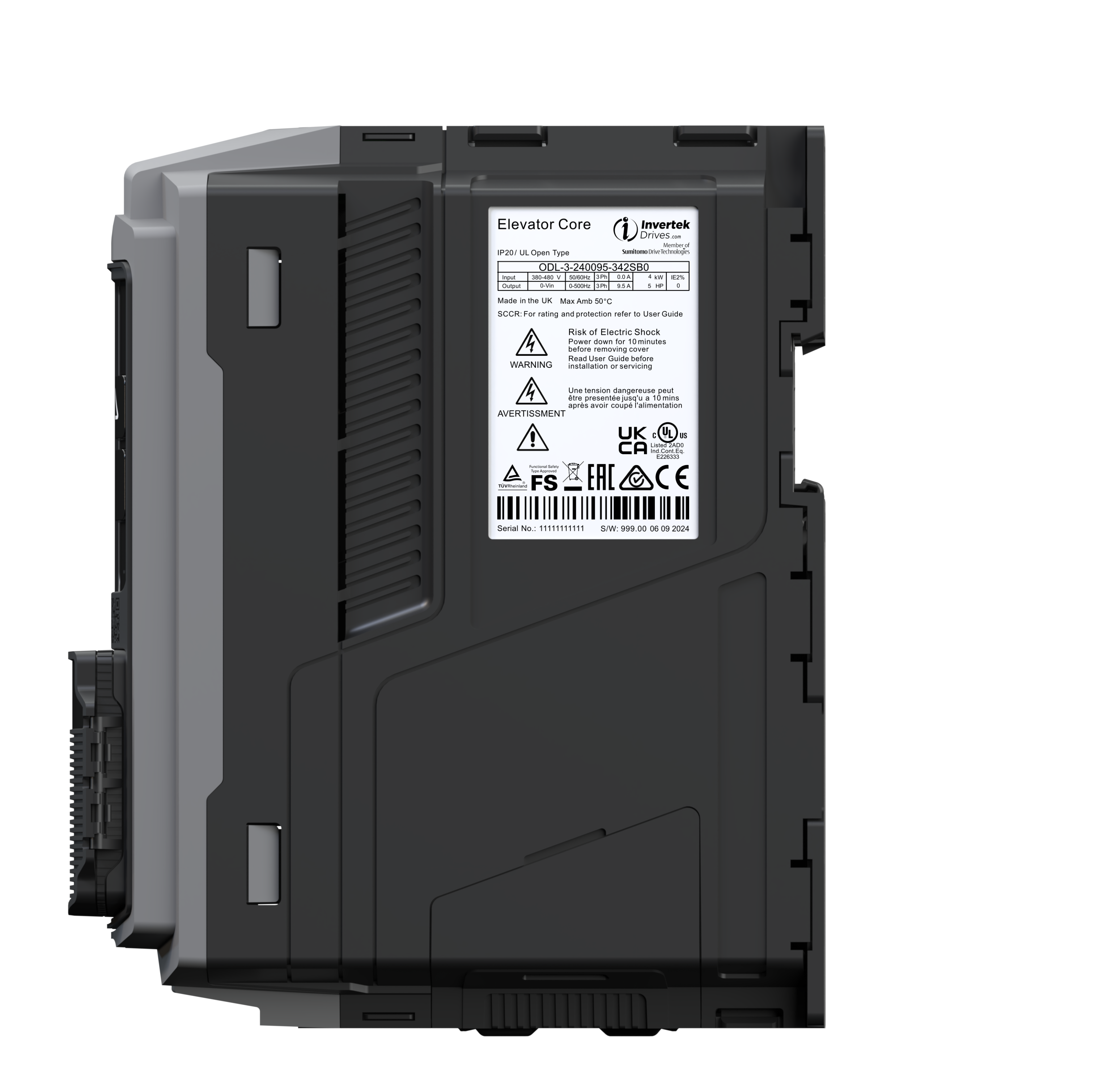
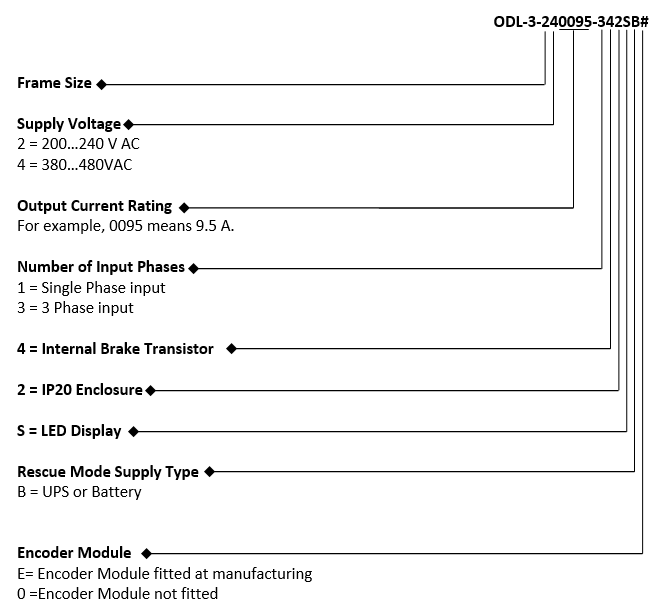
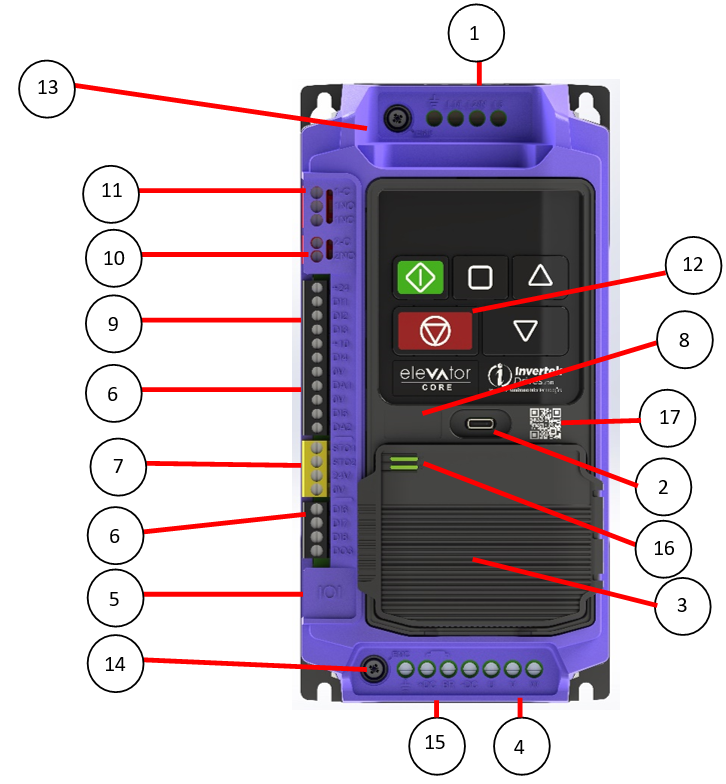
Label | Description |
---|---|
1 | Power Supply Input Terminals |
2 | USB-C Port -Used to light up the drive display and allow drive programming and parameter viewing using a device with USB-C output |
3 | Optional Universal Encoder Module for closed loop operation |
4 | Motor Connection Terminals |
5 | RJ45 Port for Modbus RTU / CAN open / PC interface (NOT FOR ETHERNET!) |
6 | Digital Inputs/Outputs |
7 | Safe Torque-Off Inputs |
8 | Drive Serial Number and Rating |
9 | Digital,Analogue Inputs/Outputs |
10 | Motor Brake Control Output |
11 | Motor Contactor Control Output (Default Function) |
12 | Trip reset Button (In addition to terminal & network reset) |
13 | Input EMC Filter and Varistor Circuit to earth Disconnect |
14 | DC Link EMC Filter Circuit to earth Disconnect |
15 | Brake Resistor Connection Terminals (Only Connect brake resistor between +DC and BR) |
16 | Encoder Status LED’s |
17 | QR Code for on-line support documentation |
Technical Data
The information provided in the following sections must be adhered to, operating the drive outside of the limits set out could result in incorrect operation of the drive and/or damage to the drive/connected equipment.
200-240V ±10% - 1 Phase Input
Model Code | Power Rating | Frame Size | Input Current A | Fuse or MCB (Type B) | Maximum Supply/Motor Cable Size | Rated Output Current A | Overload | Recommended Brake Resistance Ω (Minimum) | *Resistor power rating (W) | |||
kW | HP | Non UL | UL | mm | AWG/ kcmil | |||||||
2.2 | 3 | 2 | 22 | 25 | 25 | 6 | 10 | 10.5 | 150% 60 sec's / 200% 2 sec's | 35 (20) | 1000 |
200 – 240 Volt (+/-10%), 3 Phase Input (50-60Hz +/- 5%)
Model Code | Power Rating | Frame Size | Input Current A | Fuse or MCB (Type B) | Maximum Supply/Motor Cable Size | Rated Output Current A | Overload | Recommended Brake Resistance Ω (Minimum) | *Resistor power rating (W) | |||
kW | HP | Non UL | UL | mm | AWG/ kcmil | |||||||
4 | 5 | 2 | 22 | 25 | 30 | 6 | 10 | 18 | 150% 60 sec's / 200% 2 sec's | 20 (20) | 1000 | |
5.5 | 7.5 | 2 | 27 | 32 | 35 | 6 | 10 | 24 | 20 (20) | 150 | ||
7.5 | 10.0 | 3 | 34 | 40 | 40 | 16 | 6 | 30.0 | 20 (12) | 2000 |
380 – 480 Volt (+/-10%), 3 Phase Input (50-60Hz +/- 5%)
Model Code | Power Rating | Frame Size | Input Current A | Fuse or MCB (Type B) | Maximum Supply/Motor Cable Size | Rated Output Current A | Overload | Recommended Brake Resistance Ω (Minimum) | *Resistor power rating (W) | |||
kW | HP | Non UL | UL | mm | AWG/ kcmil | |||||||
4 | 5 | 2 | 14 | 16 | 20 | 6 | 10 | 9.5 | 150% 60 sec's / 200% 2 sec's | 100 (40) | 1000 | |
5.5 | 7.5 | 2 | 21 | 32 | 30 | 6 | 10 | 14 | 75 (40) | 1500 | ||
7.5 | 10 | 3 | 24 | 32 | 35 | 16 | 6 | 18 | 50 (22) | 2000 | ||
11 | 15 | 3 | 30 | 40 | 40 | 16 | 6 | 24 | 40 (22) | 3000 | ||
15 | 20 | 3 | 38 | 50 | 60 | 16 | 6 | 30.0 | 50 (22) | 4000 |
Mains Input Voltage Requirements
Depending upon model and power rating, the drives are designed for direct connection to the following supplies:
Model Number | Supply Voltage | Phases | Frequency |
---|---|---|---|
ODL-3-x4xxx-3xxxx | 380 – 480 Volts + / - 10% | 3 | 50 – 60Hz + / - 5% |
ODL-3-x2xxx-3xxxx | 200 – 240 Volts + / - 10% | 3 | 50 – 60Hz + / - 5% |
ODL-3-x2xxx-1xxxx | 200 – 240 Volts + / - 10% | 1 | 50 – 60Hz + / - 5% |
All 3 phase input drives have phase imbalance monitoring. A phase imbalance of > 3% will result in the drive tripping. For input supplies which have supply imbalance greater than 3% (typically the Indian sub- continent & parts of Asia Pacific including China) Invertek Drives recommends the installation of input line reactors.
Rescue Mode Voltage Requirements when operating with a UPS
Rescue Mode Voltage Requirements when operating with Batteries
Continuous Current Ratings
Ratings shown below apply to a maximum of 50°C ambient temperature at 10kHs switching frequency.
200-240V ±10% - 1 Phase Input | ||||
---|---|---|---|---|
Model Number | kW | HP | Output Current (A) | Frame Size |
ODL-3-220105-142SB# | 2.2 | 3 | 10.5 | 2 |
200-240V ±10% - 3 Phase Input | ||||
---|---|---|---|---|
Model Number | kW | HP | Output Current (A) | Frame Size |
ODL-3-220180-342SB# | 4 | 5 | 18 | 2 |
ODL-3-220240-342SB# | 5.5 | 7.5 | 24 | 2 |
ODL-3-320300-342SB# | 7.5 | 10 | 30 | 3 |
380-480V ±10% - 3 Phase Input | ||||
---|---|---|---|---|
Model Number | kW | HP | Output Current (A) | Frame Size |
ODL-3-240095-342SB# | 4 | 5 | 9.5 | 2 |
ODL-3-240140-342SB# | 5.5 | 7.5 | 14 | 2 |
ODL-3-340180-342SB# | 7.5 | 10 | 18 | 3 |
ODL-3-340240-342SB# | 11 | 15 | 24 | 3 |
ODL-3-340300-F42SB# | 15 | 20 | 30 | 3 |
Replace # with...E= for Encoder Module fitted at manufacturing or 0 = for Encoder Module not fitted in manufacturing.
Overload Current Ratings
The drive has an overload capacity of 150% for 60 seconds and 200% for 3 seconds.
Environmental
Ambient temperature range:
Operational : -20 … 50°C
Storage and Transportation : -40 °C … 60 °C
Max altitude for rated operation : 1000m
For operation above 1000m the drive maximum output current needs to be reduced by 1% per 100m / 328ft
Installation above 2000m/6562ft is not UL approved
Relative Humidity : < 95% (non-condensing)
Note : Drive must be Frost and moisture free at all times
Parameter Table Overview
All parameters are listed with their associated information. The links below will take you to each Group.
Group 1 User IO - Parameter List
Parameter Number | Parameter Name | Units | Default | Available Settings | Access | Change During Run | Scaling | Size (Bytes) | CAN Register | CAN Sub Index | Modbus Register | ||||||||||||||||||||||||||||||||||||||||||||||||||||||||||||||
---|---|---|---|---|---|---|---|---|---|---|---|---|---|---|---|---|---|---|---|---|---|---|---|---|---|---|---|---|---|---|---|---|---|---|---|---|---|---|---|---|---|---|---|---|---|---|---|---|---|---|---|---|---|---|---|---|---|---|---|---|---|---|---|---|---|---|---|---|---|---|---|---|---|
P1-01 | Primary Command Source | N/A | 0 : Terminal | 0 : Terminal 1 : Modbus-RTU 2 : CANopen | RW | N | N/A | 1 | 2065h | 0 | 101 | ||||||||||||||||||||||||||||||||||||||||||||||||||||||||||||||
Select the command source for the drive.
| |||||||||||||||||||||||||||||||||||||||||||||||||||||||||||||||||||||||||
P1-02 | Control Terminal Function Select | N/A | 1 : Macro 1 | 0 : Macro 0 1 : Macro 1 2 : Macro 2 3 : Macro 3 4 : Macro 4 5 : Macro 5 6 : Macro 6 7 : Macro 7 8 : Macro 8 9 : Macro 9 10 : Macro 10 11 : Macro 11 | RW | N | N/A | 1 | 2066h | 0 | 102 | ||||||||||||||||||||||||||||||||||||||||||||||||||||||||||||||
When the Primary Command Source (P1-01) is set to 0 the setting of Parameter P1-02 defines the function of each of the drives control terminals. Use the Macro table found in Control Terminal Function Select Macros to decide the function of each Control Terminal input. NoteThe status of the control terminals can be monitored using parameter P0-01 and P0-02The status of the control terminals can be monitored using parameter P0-01 and P0-02. | |||||||||||||||||||||||||||||||||||||||||||||||||||||||||||||||||||||||||
P1-03 | DI4 Analog Input 1 Format | N/A | U 0-10 | See Table | RW | N | N/A | 1 | 2067h | 0 | 103 | ||||||||||||||||||||||||||||||||||||||||||||||||||||||||||||||
Terminal DI4 can operate from either a Digital Input signal or Analog Input signal, this parameter allows the Analog Format to be selected for analog operation.
| |||||||||||||||||||||||||||||||||||||||||||||||||||||||||||||||||||||||||
P1-04 | DI4 Analog Input 1 Offset | % | 0.0% | -500.0 ... 500.0 % | RW | Y | 1 = 0.1% | 2 | 2068h | 0 | 104 | ||||||||||||||||||||||||||||||||||||||||||||||||||||||||||||||
When Terminal DI4 is operating as an Analog input this parameter allows an offset to be set, the value is set as a percentage of the full-scale range of the input, which is applied to the analog input signal | |||||||||||||||||||||||||||||||||||||||||||||||||||||||||||||||||||||||||
P1-05 | DI4 Analog Input 1 Scaling | % | 100.0% | -500.0 ... 500.0 % | RW | Y | 1 = 0.1% | 2 | 2069h | 0 | 105 | ||||||||||||||||||||||||||||||||||||||||||||||||||||||||||||||
When Terminal DI4 is operating as an analogue input Scales the analog input by this factor, e.g. if P1-03 is set for 0 – 10, and the scaling factor is set to 200.0%, a 5 volt input at the control terminal DI4 will result in the drive running at maximum speed (P8- 01). The pre and post scaling values can be viewed in parameters P0-56 and P0-57 | |||||||||||||||||||||||||||||||||||||||||||||||||||||||||||||||||||||||||
P1-06 | DI4 Analog Input 1 Filter | sec | 0.00s | 0.00 ... 2.00 s | RW | Y | 1 = 0.01 s | 1 | 206Ah | 0 | 106 | ||||||||||||||||||||||||||||||||||||||||||||||||||||||||||||||
This filter helps in situations where the analog input is used for the speed reference or from a Torque sensor and the source signal is noisy which would result in oscillation in speed. The filters primary aim is to make the signal smoother to the internal speed reference but will result in less responsiveness. | |||||||||||||||||||||||||||||||||||||||||||||||||||||||||||||||||||||||||
P1-07 | DI4 Analog Input Signal Loss Reaction | N/A | 0 : No Reaction | See Table | RW | Y | N/A | 1 | 206Bh | 0 | 107 | ||||||||||||||||||||||||||||||||||||||||||||||||||||||||||||||
The drive will monitor for speed reference signal loss on the analog input terminals and react according to the setting of P1-07. Speed reference loss is defined as the point when the speed reference falls below a % (as per set in P1-08) of the previous reference for a period of 500ms.
| |||||||||||||||||||||||||||||||||||||||||||||||||||||||||||||||||||||||||
P1-08 | DI4/DI5 Analog Input Signal Loss Speed | % | 80.00% | 0.00 ... 100.00 % | RW | Y | 1 = 0.01% | 1 | 206Ch | 0 | 108 | ||||||||||||||||||||||||||||||||||||||||||||||||||||||||||||||
Used in conjunction with P1-07 (DI4/DI5 Analog Input Signal Loss Reaction) and P1-13 (Analog Input 2) Signal Loss Reaction setting 1 and is set as a % of the speed reference prior to the speed reference loss. | |||||||||||||||||||||||||||||||||||||||||||||||||||||||||||||||||||||||||
P1-09 | DI5 Analog Input 2 Format | N/A | U 0-10 | See Table | RW | Y | N/A | 1 | 206Dh | 0 | 109 | ||||||||||||||||||||||||||||||||||||||||||||||||||||||||||||||
| |||||||||||||||||||||||||||||||||||||||||||||||||||||||||||||||||||||||||
P1-10 | DI5 Analog Input 2 Offset | % | 0.0% | -500.0 ... 500.0 % | RW | Y | 1 = 0.1% | 2 | 206Eh | 0 | 110 | ||||||||||||||||||||||||||||||||||||||||||||||||||||||||||||||
When terminal DI5 is operating as an Analog input this parameter sets an offset, as a percentage of the full-scale range of the input, which is applied to the analog input signal. | |||||||||||||||||||||||||||||||||||||||||||||||||||||||||||||||||||||||||
P1-11 | DI5 Analog Input 2 Scaling | % | 100.0% | -500.0 ... 500.0 % | RW | Y | 1 = 0.1% | 2 | 206Fh | 0 | 111 | ||||||||||||||||||||||||||||||||||||||||||||||||||||||||||||||
When Terminal DI4 is operating as an analogue input Scales the analog input by this factor, e.g. if P1-03 is set for 0 – 10, and the scaling factor is set to 200.0%, a 5 volt input at the control terminal DI4 will result in the drive running at maximum speed (P8- 01). The pre and post scaling values can be viewed in parameters P0-58 and P0-59. | |||||||||||||||||||||||||||||||||||||||||||||||||||||||||||||||||||||||||
P1-12 | DI5 Analog Input 2 Filter | sec | 0.00s | 0.00 ... 2.00 s | RW | Y | 1 = 0.01 s | 1 | 2070h | 0 | 112 | ||||||||||||||||||||||||||||||||||||||||||||||||||||||||||||||
This filter helps in situations where the analog input is used for the speed reference or from a Torque sensor and the source signal is noisy which would result in oscillation in speed. The filters primary aim is to make the signal smoother to the internal speed reference but will result in less responsiveness. | |||||||||||||||||||||||||||||||||||||||||||||||||||||||||||||||||||||||||
P1-13 | DI5 Analog Input 2 Signal Loss Reaction | N/A | 0 : No Reaction | See Table | RW | Y | N/A | 1 | 2071h | 0 | 113 | ||||||||||||||||||||||||||||||||||||||||||||||||||||||||||||||
Set the reaction method on a signal loss when DI5 is used as analogue input speed reference
| |||||||||||||||||||||||||||||||||||||||||||||||||||||||||||||||||||||||||
P1-14 | DA1 Output 1 Type | N/A | 0 : Digital Output | See Table | RW | Y | N/A | 1 | 2072h | 0 | 114 | ||||||||||||||||||||||||||||||||||||||||||||||||||||||||||||||
Sets if the output terminal DA1 is to operate as a Digital Output (24Vdc) or as an Analog Output, the Analog type is defined in P1-18 DA1 Analog Output 1 Format.
| |||||||||||||||||||||||||||||||||||||||||||||||||||||||||||||||||||||||||
P1-15 | DA1 Digital Output 1 Function Select | N/A | 1 | See Table | RW | Y | N/A | 1 | 2073h | 0 | 115 | ||||||||||||||||||||||||||||||||||||||||||||||||||||||||||||||
| |||||||||||||||||||||||||||||||||||||||||||||||||||||||||||||||||||||||||
P1-16 | DA1 Digital Output 1 Invert | N/A | 0 : Standard | 0 : Standard 1 : Inverted | RW | Y | N/A | 1 | 2074h | 0 | 116 | ||||||||||||||||||||||||||||||||||||||||||||||||||||||||||||||
Inverts the logic of DA1 output when operating in digital output mode | |||||||||||||||||||||||||||||||||||||||||||||||||||||||||||||||||||||||||
P1-17 | DA1 Analog Output 1 Source Select | N/A | 0 : Output Frequency | See Table | RW | Y | N/A | 1 | 2075h | 0 | 117 | ||||||||||||||||||||||||||||||||||||||||||||||||||||||||||||||
| |||||||||||||||||||||||||||||||||||||||||||||||||||||||||||||||||||||||||
P1-18 | DA1 Analog Output 1 Source Select | N/A | U 0-10 | See Table | RW | Y | N/A | 1 | 2076h | 0 | 118 | ||||||||||||||||||||||||||||||||||||||||||||||||||||||||||||||
| |||||||||||||||||||||||||||||||||||||||||||||||||||||||||||||||||||||||||
P1-19 | DA1 Analog Output 1 Scaling | % | 100.0% | 0.0 ... 500.0 % | RW | Y | 1 = 0.1% | 1 | 2077h | 0 | 119 | ||||||||||||||||||||||||||||||||||||||||||||||||||||||||||||||
Defines the scaling percentage. | |||||||||||||||||||||||||||||||||||||||||||||||||||||||||||||||||||||||||
P1-20 | DA1 Analog Output 1 Offset | % | 0.0% | -500.0 ... 500.0 % | RW | Y | 1 = 0.1% | 2 | 2078h | 0 | 120 | ||||||||||||||||||||||||||||||||||||||||||||||||||||||||||||||
Defines the scaling factor as a %, where output value = (Input value-Offset P1-20) *Scaling factor P1-19 | |||||||||||||||||||||||||||||||||||||||||||||||||||||||||||||||||||||||||
P1-21 | DA2 Output 2 Type | N/A | 0 : Digital Output | See Table | RW | Y | N/A | 1 | 2079h | 0 | 121 | ||||||||||||||||||||||||||||||||||||||||||||||||||||||||||||||
Sets if the output from terminal DA2 is to operate as a digital output (24V dc) or as an Analog Output, the Analog type is defined in P1-25 DA2 Analog Output 2 Format.
| |||||||||||||||||||||||||||||||||||||||||||||||||||||||||||||||||||||||||
P1-22 | DA2 Digital Output 2 Function Select | N/A | 0 | See Table | RW | Y | N/A | 1 | 207Ah | 0 | 122 | ||||||||||||||||||||||||||||||||||||||||||||||||||||||||||||||
This defines the output source when DA2 is configured in digital mode.
| |||||||||||||||||||||||||||||||||||||||||||||||||||||||||||||||||||||||||
P1-23 | DA2 Digital Output 2 Invert | N/A | 0 : Standard | 0 : Standard 1 : Inverted | RW | Y | N/A | 1 | 207Bh | 0 | 123 | ||||||||||||||||||||||||||||||||||||||||||||||||||||||||||||||
Inverts the logic of DA2 output when operating in digital output mode. | |||||||||||||||||||||||||||||||||||||||||||||||||||||||||||||||||||||||||
P1-24 | DA2 Analogue Output 2 Source Select | N/A | 0 : Output Frequency | See Table | RW | Y | N/A | 1 | 207Ch | 0 | 124 | ||||||||||||||||||||||||||||||||||||||||||||||||||||||||||||||
This defines the output source when DA2 is configured in analogue mode.
| |||||||||||||||||||||||||||||||||||||||||||||||||||||||||||||||||||||||||
P1-25 | DA2 Analog Output 2 Format | N/A | U 0-10 | See Table | RW | Y | N/A | 1 | 207Dh | 0 | 125 | ||||||||||||||||||||||||||||||||||||||||||||||||||||||||||||||
Defines the format of Analog Output 2
| |||||||||||||||||||||||||||||||||||||||||||||||||||||||||||||||||||||||||
P1-26 | DA2 Analog Output 2 Scaling | % | 100.0% | 0.0 ... 500.0 % | RW | Y | 1 = 0.1% | 2 | 207Eh | 0 | 126 | ||||||||||||||||||||||||||||||||||||||||||||||||||||||||||||||
Defines the scaling percentage. | |||||||||||||||||||||||||||||||||||||||||||||||||||||||||||||||||||||||||
P1-27 | DA2 Analog Output 2 Offset | % | 0.0% | -500.0 ... 500.0 % | RW | Y | 1 = 0.1% | 2 | 207Fh | 0 | 127 | ||||||||||||||||||||||||||||||||||||||||||||||||||||||||||||||
Defines the scaling factor as a %, where output value = (Input value-Offset P1-27)*Scaling factor P1-26 | |||||||||||||||||||||||||||||||||||||||||||||||||||||||||||||||||||||||||
P1-28 | DO3 Digital Output 3 Function Select | N/A | 12 : Motor Shorting Contactor | See Table | RW | Y | N/A | 1 | 2080h | 0 | 128 | ||||||||||||||||||||||||||||||||||||||||||||||||||||||||||||||
| |||||||||||||||||||||||||||||||||||||||||||||||||||||||||||||||||||||||||
P1-29 | DO3 Digital Output 3 Invert | N/A | 0 : Standard | 0 : Standard 1 : Inverted | RW | Y | N/A | 1 | 2081h | 0 | 129 | ||||||||||||||||||||||||||||||||||||||||||||||||||||||||||||||
Inverts the logic of DO3 output. | |||||||||||||||||||||||||||||||||||||||||||||||||||||||||||||||||||||||||
P1-30 | Relay 1 Function Select | N/A | 11 : Motor Contactor Control | See Table | RW | Y | N/A | 1 | 2082h | 0 | 130 | ||||||||||||||||||||||||||||||||||||||||||||||||||||||||||||||
| |||||||||||||||||||||||||||||||||||||||||||||||||||||||||||||||||||||||||
P1-31 | DA1 Threshold Upper Limit | % | 100.0% | 0.0 ... 200.0 % | RW | Y | 1 = 0.1% | 1 | 2083h | 0 | 131 | ||||||||||||||||||||||||||||||||||||||||||||||||||||||||||||||
Used in conjunction with settings 5,6,7,10 of Parameter P1-15 DA1 Digital Output 1 Function Select | |||||||||||||||||||||||||||||||||||||||||||||||||||||||||||||||||||||||||
P1-32 | DA1 Threshold Lower Limit | % | 0.0% | 0.0 ... 100.0 % | RW | Y | 1 = 0.1% | 1 | 2084h | 0 | 132 | ||||||||||||||||||||||||||||||||||||||||||||||||||||||||||||||
Used in conjunction with settings 5,6,7,10 of Parameter P1-15 DA1 Digital Output 1 Function Select | |||||||||||||||||||||||||||||||||||||||||||||||||||||||||||||||||||||||||
P1-33 | DA2 Threshold Upper Limit | % | 100.0% | 0.0 ... 200.0 % | RW | Y | 1 = 0.1% | 1 | 2085h | 0 | 133 | ||||||||||||||||||||||||||||||||||||||||||||||||||||||||||||||
Used in conjunction with settings 5,6,7,10 of Parameter P1-22 DA1 Digital Output 2 Function Select | |||||||||||||||||||||||||||||||||||||||||||||||||||||||||||||||||||||||||
P1-34 | DA2 Threshold Lower Limit | % | 0.0% | 0.0 ... 100.0 % | RW | Y | 1 = 0.1% | 1 | 2086h | 0 | 134 | ||||||||||||||||||||||||||||||||||||||||||||||||||||||||||||||
Used in conjunction with settings 5,6,7,10 of Parameter P1-22 DA1 Digital Output 2 Function Select | |||||||||||||||||||||||||||||||||||||||||||||||||||||||||||||||||||||||||
P1-35 | Relay 1 Threshold Upper Limit | % | 100.0% | 0.0 ... 200.0 % | RW | Y | 1 = 0.1% | 1 | 2087h | 0 | 135 | ||||||||||||||||||||||||||||||||||||||||||||||||||||||||||||||
Used in conjunction with settings 5,6,7,10 of Parameter P1-30 (Relay 1 Source Selector) | |||||||||||||||||||||||||||||||||||||||||||||||||||||||||||||||||||||||||
P1-36 | Relay 1 Threshold Lower Limit | % | 0.0% | 0.0 ... 100.0 % | RW | Y | 1 = 0.1% | 1 | 2088h | 0 | 136 | ||||||||||||||||||||||||||||||||||||||||||||||||||||||||||||||
Used in conjunction with settings 5,6,7,10 of Parameter P1-30 (Relay 1 Source Selector) | |||||||||||||||||||||||||||||||||||||||||||||||||||||||||||||||||||||||||
P1-37 | Digital/Relay Output Hysteresis Band | % | 0.3% | 0.0 ... 25.0 % | RW | Y | 1 = 0.1% | 1 | 2089h | 0 | 137 | ||||||||||||||||||||||||||||||||||||||||||||||||||||||||||||||
This parameter works in conjunction with P1-15, P1-22, P1-28, P1-30 = 2 or 3 to set a band around the Motor at Target Speed (e.g. P1-15 = 3) or Motor at Zero speed (e.g. P1-15 = 2). When the speed is within this band, the drive is considered to be at Target speed or Zero speed. This function is used to prevent “chatter” on the relay/Digital output if the operating speed coincides with the level at which the digital / relay output changes state. e.g. if P1-30 = 3, P8-01 = 50Hz and P1-36 = 5%, the relay contacts close above 2.5Hz. | |||||||||||||||||||||||||||||||||||||||||||||||||||||||||||||||||||||||||
P1-38 | DO3 Threshold Upper Limit | % | 100.0% | 0.0 ... 200.0 % | RW | Y | 1 = 0.1% | 1 | 208Ah | 0 | 138 | ||||||||||||||||||||||||||||||||||||||||||||||||||||||||||||||
Used in conjunction with settings 5,6,7,10 of Parameter P1-28 DO3 Digital Output 3 Function Select to set the upper limit of the threshold. | |||||||||||||||||||||||||||||||||||||||||||||||||||||||||||||||||||||||||
P1-39 | DO3 Threshold Lower Limit | % | 0.0% | 0.0 ... 100.0 % | RW | Y | 1 = 0.1% | 1 | 208Bh | 0 | 139 | ||||||||||||||||||||||||||||||||||||||||||||||||||||||||||||||
Used in conjunction with settings 5,6,7,10 of Parameter P1-28 DO3 Digital Output 3 Function Select to set the lower limit of the threshold. | |||||||||||||||||||||||||||||||||||||||||||||||||||||||||||||||||||||||||
P1-40 | Start Mode Select / Automatic Restart | N/A | 0 : Edge-r | See Table | RW | Y | N/A | 1 | 208Ch | 0 | 140 | ||||||||||||||||||||||||||||||||||||||||||||||||||||||||||||||
Defines the behaviour of the drive relating to the Direction /Enable digital input and configures the Automatic Restart function.
NoteThis parameter is only applicable if the other run conditions are fulfilled. For example even if P1-40 is set to Auto-0 and the direction input is closed the drive will not start if the Safety Chain is not closed. | |||||||||||||||||||||||||||||||||||||||||||||||||||||||||||||||||||||||||
P1-41 | Auto-reset delay time | sec | 20s | 1 ... 60 s | RW | Y | N/A | 1 | 208Dh | 0 | 141 | ||||||||||||||||||||||||||||||||||||||||||||||||||||||||||||||
Sets the delay time which will elapse between consecutive drive reset attempts when Auto Reset is enabled in P1-40 | |||||||||||||||||||||||||||||||||||||||||||||||||||||||||||||||||||||||||
P1-42 | Speed Following Error | % | 5.0% | 0.0...50.0% | RW | Y | 1 = 0.1% | 2 | 208Eh | 0 | 142 | ||||||||||||||||||||||||||||||||||||||||||||||||||||||||||||||
Used in conjunction with P1-15, P1-22, P1-28 and P1-30 setting 19 as the % error difference between set speed and the actual speed (estimated speed in open loop/encoder speed in closed loop-with encoder) | |||||||||||||||||||||||||||||||||||||||||||||||||||||||||||||||||||||||||
P1-43 | Positive/Negative Logic Select | N/A | 0 : Positive Logic | 0 : Positive Logic 1 : Negative Logic | RW | N | N/A | 1 | 208Fh | 0 | 143 | ||||||||||||||||||||||||||||||||||||||||||||||||||||||||||||||
Changes the control logic for all digital inputs (including the Universal Encoder module Daux1 and Daux2),
NoteSTO1 and STO2 Inputs are always positive logic. |
Control Terminal Function Select Macros
When the Primary Command Source (P1-01) is set to 0, the setting of Parameter P1-02 defines the function of each of the drives control terminals.
Use the Macro table below to select an appropriate value of P1-02 to match the elevator controller output signals.
The status of the control terminals can be monitored using parameter PP0-01 and P0-02.
P0-01 Display value | 0 | 0 | 0 | 0 | 0 |
---|---|---|---|---|---|
Function | Digital Input 1 status | Digital Input 2 status | Digital Input 3 status | Digital Input 4 status | Digital Input 5 status |
P0-02 Display value | 0 | 0 | 0 | 0 | 0 |
---|---|---|---|---|---|
Function | Digital Input 6 status | Digital Input 7 status | Digital Input 8 status | Daux 1 Input Status | Daux 2 Input Status |
The Macro tables are used by P1-02 to select the function of each IO Input. P1-02 parameter can be found here.
P1-02 Setting | DI1 | DI2 | DI3 | DI4 | DI5 | DI6 | DI7 | DI8 | Speed Source |
---|---|---|---|---|---|---|---|---|---|
1 | Open = Disabled Closed = Run Forward | Open = Disabled Closed = Run Reverse | Open = Disabled Closed = Levelling Speed (P8-05) | Open = Disabled Closed = High Speed (P8-06) | Open = Disabled Closed = High Speed 5/Relevelling Speed (P8-12) | Open = Disabled Closed = Inspection Speed (P8-08) | Fault Reset | Open = Mains Mode Closed = Rescue Mode Activate | If more than 1 speed selection input is high the highest speed will be used. |
2 | Open = Disabled Closed = Run Forward | Open = Disabled Closed = Run Reverse | Open = Disabled Closed = Levelling Speed (P8-05) | Open = Disabled Closed = High Speed (P8-06) | Open Available Functions =
Closed = Ok | Open = Disabled Closed = Inspection Speed (P8-08) | Fault Reset | Open = Mains Mode Closed = Rescue Mode Activate | |
For settings 1 and 2 above, the drive will only start if all the below conditions are met:
| |||||||||
3 | Open = Disabled Closed = Run Forward | Open = Disabled Closed = Run Reverse | 1 | 0 | 0 | Open Available Functions =
Closed = Ok | Fault Reset | Open = Mains Mode Closed = Rescue Mode Activate | P8-06 High Speed |
0 or 1 | 0 | 1 | P8-07 Intermediate Speed | ||||||
0 or 1 | 1 | 0 or 1 | P8-08 Inspection Speed | ||||||
0 | 0 | 0 | P8-05 Levelling Speed | ||||||
4 | Open = Disabled Closed = Run Forward | Open = Disabled Closed = Run Reverse | 1 | 0 | Open Available Functions =
Closed = Ok | 0 | Fault Reset | Open = Mains Mode Closed = Rescue Mode Activate | P8-06 High Speed |
0 or 1 | 0 | 1 | P8-07 Intermediate Speed | ||||||
0 or 1 | 1 | 0 or 1 | P8-08 Inspection Speed | ||||||
0 | 0 | 0 | P8-05 Levelling Speed | ||||||
5 | Open = Disabled Closed = Run Forward | Open = Disabled Closed = Run Reverse | 0 | 0 | 0 | Open Available Functions =
Closed = Ok | Fault Reset | Open = Mains Mode Closed = Rescue Mode Activate | P8-05 Levelling Speed |
1 | 0 | 0 | P8-06 High Speed | ||||||
0 | 1 | 0 | P8-07 Intermediate Speed | ||||||
1 | 1 | 0 | P8-08 Inspection Speed | ||||||
0 | 0 | 1 | P8-09 Speed 2 | ||||||
1 | 0 | 1 | P8-10 Speed 3 | ||||||
0 | 1 | 1 | P8-11 Speed 4 | ||||||
1 | 1 | 1 | P8-12 High Speed 5/Relevelling Speed | ||||||
6 | Open = Disabled Closed = Run Forward | Open = Disabled Closed = Run Reverse | No Function | Speed Reference from Analogue input | Open Available Functions =
Closed = Ok | Open Available Functions =
Closed = Ok | Fault Reset | Open = Mains Mode Closed = Rescue Mode Activate | Analogue input Reference level |
7 | Open = Disabled Closed = Run Forward | Open = Disabled Closed = Run Reverse | Open = Disabled Closed = Levelling Speed (P8-05) | Torque Sensor Input | Open = Disabled Closed = High Speed (P8-06) | Open = Disabled Closed = Inspection Speed (P8-08) | Fault Reset | Open = Mains Mode Closed = Rescue Mode Activate | If more than 1 speed selection input is high the highest speed will be used. |
For setting 7 above, the drive will only start if all the below conditions are met:
| |||||||||
8 | Open = Disabled Closed = Run Forward | Open = Disabled Closed = Run Reverse | 0 | 0 | Brake Release Monitor Input 1 (Only Active if P5-04 Brake Release Monitoring Enable is set to a value of 2) | Brake Release Monitor Input 2 (Only Active if P5-04 Brake Release Monitoring Enable is set to a value of 2) | Fault Reset | Open = Mains Mode Closed = Rescue Mode Activate | P8-05 Levelling Speed |
1 | 0 | P8-06 High Speed | |||||||
0 | 1 | P8-07 Intermediate Speed | |||||||
1 | 1 | P8-08 Inspection Speed | |||||||
9 | Open = Disabled Closed = Run Forward | Open = Disabled Closed = Run Reverse | Open = Mains Mode Closed = Rescue Mode Activate | 0 | 0 | 0 | Brake Release Monitor Input 1 (Only Active if P5-04 Brake Release Monitoring Enable is set to a value of 2) | Open = Disabled Closed = Drive Enabled | P8-05 Levelling Speed |
1 | 0 | 0 | P8-06 High Speed | ||||||
0 | 1 | 0 | P8-07 Intermediate Speed | ||||||
1 | 1 | 0 | P8-08 Inspection Speed | ||||||
0 | 0 | 1 | P8-09 Speed 2 | ||||||
1 | 0 | 1 | P8-10 Speed 3 | ||||||
0 | 1 | 1 | P8-11 Speed 4 | ||||||
1 | 1 | 1 | P8-12 High Speed 5/Relevelling Speed | ||||||
For setting 9 above only, the motor contactor relay will close, and normal contactor sequence will begin when a direction has been selected, however the drive will not start until Digital Input 8 (Drive Enable signal has been given) | |||||||||
10 | Open = Disabled Open = Disabled | Open = Disabled Closed = Run Reverse | 0 | 0 | Open Available Functions =
Closed = Ok | Open Available Functions =
Closed = Ok | Open Available Functions =
Closed = Ok | Open = Mains Mode Closed = Rescue Mode Activate | P8-05 Levelling Speed |
1 | 0 | P8-06 High Speed | |||||||
0 | 1 | P8-07 Intermediate Speed | |||||||
1 | 1 | P8-08 Inspection Speed | |||||||
11 | Open = Disabled Open = Disabled | Open = Disabled Closed = Run Reverse | Open = Mains Mode Closed = Rescue Mode Activate | 0 | 0 | 0 | Brake Release Monitor Input 1 (Only Active if P5-04 Brake Release Monitoring Enable is set to a value of 2) | No Function | P8-05 Levelling Speed |
1 | 0 | 0 | P8-06 High Speed | ||||||
0 | 1 | 0 | P8-07 Intermediate Speed | ||||||
1 | 1 | 0 | P8-08 Inspection Speed | ||||||
0 | 0 | 1 | P8-09 Speed 2 | ||||||
1 | 0 | 1 | P8-10 Speed 3 | ||||||
0 | 1 | 1 | P8-11 Speed 4 | ||||||
1 | 1 | 1 | P8-12 High Speed 5/Relevelling Speed | ||||||
For setting 11 above only, the motor contactor relay will close, and normal contactor sequence will begin when a direction has been selected. |
Group 2 Communications - Parameter List
Parameter Number | Parameter Name | Units | Default | Available Settings | Access | Change During Run | Scaling | Size (Bytes) | CAN Register | CAN Sub Index | Modbus Register |
---|---|---|---|---|---|---|---|---|---|---|---|
P2-01 | Modbus Slave Address | N/A | 1 | 1...247 | RW | N | N/A | 1 | 20C9h | 0 | 201 |
Sets the drive address when communicating over Modbus-RTU via the RJ45 port on the drive. | |||||||||||
P2-02 | Modbus RTU Baud Rate | N/A | 4 : 115200bps | 0 : 9600bps 1 : 19200bps 2 : 38400bps 3 : 57600bps 4 : 115200bps | RW | N | N/A | 1 | 20Cah | 0 | 202 |
Sets the baud rate when Modbus-RTU communications is being used. | |||||||||||
P2-03 | Modbus RTU Data Format | N/A | 0 : n-1 | 0 : n-1 1 : n-2 2 : 0-1 3 : E-1 | RW | N | N/A | 1 | 20CBh | 0 | 203 |
P2-06 | Modbus RTU Response Delay | N/A | 0 char | 0 ... 16 char | RW | N | N/A | 1 | 20Ceh | 0 | 206 |
Allows the user to configure an additional delay between the drive receiving a request via the Modbus RTU interface and transmitting a reply. The value entered represents the delay in addition to the minimum delay permissible according to the Modbus RTU specification, and is expressed as the number of additional characters. | |||||||||||
P2-07 | CAN address | N/A | 1 | 1...127 | RW | N | N/A | 1 | 20CFh | 0 | 207 |
Sets the drive address when communicating over CANopen via the RJ45 port on the drive. | |||||||||||
P2-08 | CAN Baud Rate | N/A | 2 : 500kbps | 0 : 125kbps 1 : 250kbps 2 : 500kbps 3 : 1Mbps | RW | N | N/A | 1 | 20D0h | 0 | 208 |
Sets the baud rate when CANopen communications is being used. | |||||||||||
P2-09 | CAN comms lost reaction | N/A | 2: Ramp to Stop Only (No Trip) | 0 : Trip 1 : Ramp to Stop then Trip 2 : Ramp to Stop Only (No Trip) 3 : Run at Inspection Speed (P8-09) | RW | Y | N/A | 1 | 20D1h | 0 | 209 |
Controls the behaviour of the drive following a loss of communications | |||||||||||
P2-13 | USB Port Enable | N/A | 0: Disable | 0 : Disabled 1 : Enabled | RW | Y | N/A | 1 | 20D5h | 0 | 213 |
P2-20 | Modbus Messages Per Second | msg/s | 0 | 0...1000msg/s | RO | N | N/A | 2 | 20DCh | 0 | 220 |
Number of Modbus-RTU messages currently being processed per second. | |||||||||||
P2-21 | Modbus Messages Processed | N/A | 0 | 0...4294967295 | RO | N | N/A | 4 | 20DDh | 0 | 221 |
Total number of Modbus-RTU messages processed. | |||||||||||
P2-22 | Modbus Errors | N/A | 0 | 0...4294967295 | RO | N | N/A | 4 | 20Deh | 0 | 222 |
Number of Modbus-RTU messages that could not be processed due to errors. | |||||||||||
P2-23 | USB Messages Processed Per Second | msg/s | 0 | 0...1000ms | RO | N | N/A | 2 | 20DFh | 0 | 223 |
The number of messages currently being processed per second when communicating over USB-C connection. | |||||||||||
P2-24 | USB Messages Processed | N/A | 0 | 0 to 4294967295 | RO | N | N/A | 4 | 20E0h | 0 | 224 |
Total number of messages processed when communicating over USB-C | |||||||||||
P2-25 | USB Errors | N/A | 0 | 0 to 4294967295 | RO | N | N/A | 4 | 20E1h | 0 | 225 |
Number of Modbus-RTU messages that could not be processed when connected to the USB-C port. | |||||||||||
P2-50 | Modbus Control Word | N/A | 0 | 0...7 | RW | N | N/A | 1 | 20FAh | 0 | 250 |
Allows the user to Control the drive via the Modbus Control Word. | |||||||||||
P2-51 | Modbus Speed Reference | Hz | 0.00 | -P8-01 to P8-01 | RW | Y | N/A | 2 | 20FBh | 0 | 251 |
Allows the user to enter a Speed Reference for the drive to run at | |||||||||||
P2-52 | Modbus Torque Reference | % | 0.0 | 0.0 to 100.0 | RW | Y | 1 = 0.1% | 2 | 20FCh | 0 | 252 |
Allows the user to enter a Torque Reference for the drive to run at | |||||||||||
P2-53 | Modbus Ramp Rate | sec | 0.0 | 0.0 to 600.0 | RW | Y | 1 - 0.1 s | 2 | 20FDh | 0 | 253 |
Allows the user to enter a Ramp rate for the drive to accelerate/decelerate to. | |||||||||||
P2-56 | Modbus status word lower byte: Drive status | N/A | 0 | RO | N | N/A | 2 | 2100h | 0 | 256 | |
Real time Modbus Status Word lower byte. The lower byte contains drive statuses. | |||||||||||
P2-56 (1) | Modbus status word upper byte: Error code | N/A | 0 | RO | N | N/A | 2 | 2100h | 1 | ||
Real time Modbus Status Word upper byte containing the drive error code. If no error code is present the byte will show 0. | |||||||||||
P2-57 | Modbus Speed Feedback | Hz | 0.00 | RO | N | 2 | 2101h | 0 | 257 | ||
Current speed of the drive. | |||||||||||
P2-58 | Modbus Motor Current | Amps | 0.0 | RO | N | 2 | 2102h | 0 | 258 | ||
Current output current of the drive. | |||||||||||
P2-59 | Modbus Output Torque | % | 0.0 | RO | N | 2 | 2103h | 0 | 259 | ||
Current output torque of the drive. |
Group 3 System - Parameter List
Parameter Number | Parameter Name | Units | Default | Available Settings | Access | Change During Run | Scaling | Size (Bytes) | CAN Register | CAN Sub Index | Modbus Register |
---|---|---|---|---|---|---|---|---|---|---|---|
P3-01 | Motor Contactor Closing Time | sec | 0.2 s | 0.0 ...5.0 s | RW | Y | 1 = 0.1 seconds | 1 | 212Dh | 0 | 301 |
Sets a delay time between a Direction signal being applied to the drive and the drive energising the motor, this ensures that the motor contactor has had enough time to change state before current flows from the drive to the motor. Typical values are 0.2 to 0.5 seconds. During the delay time the drive will display “CC” to indicate Contactor Closing time. | |||||||||||
P3-02 | Motor Contactor-Monitoring Terminal Enable | N/A | 0 : Off | 0 : Off 1 : Enabled | RW | Y | N/A | 1 | 212Eh | 0 | 302 |
Sets Motor Contactor Monitoring to enabled or disabled. Setting 1 = Enabled Macro implications:
| |||||||||||
P3-03 | Total Number of Motor Contactor Monitoring Errors | N/A | 0 | 0...65535 | RO | N/A | N/A | 2 | 212Fh | 0 | 303 |
This value increments by 1 each time there is cF-Err error. The value can only be reset by loading factory/user defaults. | |||||||||||
P3-04 | Brake Resistor Resistance | ohms | Rating Dependent | 0...60000 ohms | RW | N/A | 2 | 2130h | 0 | 304 | |
Enter external Brake Resistor resistance in ohms. | |||||||||||
P3-05 | Brake Resistor Power | kW | 0.0 | 0.0...6000.0 kW | RW | 1 = 1 W | 2 | 2131h | 0 | 305 | |
For software protection of the connected brake resistor, enter the rated power and resistance of the resistor into the relevant parameters. The drive will then monitor the brake resistor to ensure that it does not operate outside of its designed limits. Where an external thermal protection device is fitted, and software protection is not required. Setting parameter P3-05 to zero will disable the software protection feature. | |||||||||||
P3-06 | Brake Resistor Temperature Monitor Enable | N/A | 0: Disabled | 0 : Disabled 1 : Enabled | RW | Y | N/A | 1 | 2132h | 0 | 306 |
This parameter is used when a brake resistor thermal switch is wired back to a digital input set for External trip and tells the drive that the drive should trip on a brake resistor feedback fault (Ot-br) rather than an external trip. | |||||||||||
P3-07 | Brake Resistor Temperature Monitoring trip reaction | N/A | 0 : Normal Stop, Trip After stopping | 0: Normal Stop, Trip After stopping to 1 : Immediate Trip, Apply motor Brake 2: Warning Only No Trip | RW | Y | N/A | 1 | 2133h | 0 | 307 |
This parameter defines the drive’s reaction when the Brake resistor overload function has been triggered (Ot-br) | |||||||||||
P3-08 | Sheave Diameter | N/A | 0.0 | 0.0...2000.0 | RW | Y | 1 = 0.1 | 2 | 2134h | 0 | 308 |
This defines the traction sheave diameter (<100 drive assumes inches)/(>=100 drive assumes mm) | |||||||||||
P3-09 | Roping Ratio | N/A | 1: 1:1 | 1 : 1:1 2 : 2:1 3 : 3:1 4 : 4:1 | RW | Y | N/A | 1 | 2135h | 0 | 309 |
This defines the roping ratio of the system. | |||||||||||
P3-10 | Gear Ratio | N/A | 1.0 | 1.0...100.0 | RW | Y | 10 = 1.0 | 2 | 2136h | 0 | 310 |
This defines the Gear Ratio of the mechanical Gear. | |||||||||||
P3-12 | System Inertia Constant | N/A | 60 | 0 to 100 | RW | N/A | 1 | 2138h | 0 | 312 | |
System Load Inertia to Motor Inertia Ratio entered as H= (JTot/JMot) this value can normally be left at the default value (10). |
Group 4 Motor Setup - Parameter List
Parameter Number | Parameter Name | Units | Default | Available Settings | Access | Change Run | Scaling | Size (Bytes) | CAN Register | CAN Sub Index | Modbus Register | |||||||||
---|---|---|---|---|---|---|---|---|---|---|---|---|---|---|---|---|---|---|---|---|
P4-01 | Motor Control Mode | N/A | 0: Advanced Vector IM Speed Control | 0 : Advanced Vector IM Speed Control 1 : Vector IM Speed Control 2 : Enhanced V/F IM Speed Control 3 : PM Motor Speed Control with absolute Encoder | RW | N | N/A | 1 | 2191h | 0 | 401 | |||||||||
Sets the motor control mode depending on the motor type used. | ||||||||||||||||||||
P4-02 | Motor Rated Voltage/Back EMF-PM Motors | Volts | Rating Dependent | Rating Dependent | RW | N | N/A | 1 | 2192h | 0 | 402 | |||||||||
For Induction (Geared) type elevator Motors (P4-01=0,1,2) enter the motor rated voltage as shown on the motor nameplate. o If set to 0 voltage compensation is disabled. When operating Permanent Magnet (Gearless) Motors (P4-01=3) in open loop (P6-05=0) the Phase-to-Phase back emf voltage at rated speed must be entered in this parameter. | ||||||||||||||||||||
P4-03 | Motor Rated Current | Amps | Rating Dependent | Rating Dependent | RW | N | 0.1 = 1A | 1 | 2193h | 0 | 403 | |||||||||
Enter the Rated (nameplate) current of the motor. This value must be entered to protect the motor. | ||||||||||||||||||||
P4-04 | Motor Rated Frequency | Hz | 50.00 | 5.00 ... 500.00 Hz | RW | N | 1 = 100 Hz | 2 | 2194h | 0 | 404 | |||||||||
Rated (nameplate) Frequency of the motor. | ||||||||||||||||||||
P4-05 | Motor Poles | N/A | 4 | 0...240 | RW | N | N/A | 1 | 2195h | 0 | 405 | |||||||||
Enter the number of motor poles as shown on the motor nameplate.
| ||||||||||||||||||||
P4-06 | Motor Rated Speed | rpm | 0 | 0 to 3000 | RW | N | 1 = 1rpm | 2 | 2196h | 0 | 406 | |||||||||
Rated (nameplate) speed of the motor. IM motor: Allows drive calculation of the rated slip of the motor (in V/F Mode only) All motors: Changes all speed related parameter values to rpm vs Hz and also required for operating in Linear units mode and when operating with an Encoder. | ||||||||||||||||||||
P4-07 | Motor Power Factor | N/A | 0.80 | 0.00 to 0.99 | RW | N | 1 = 0.01 | 1 | 2197h | 0 | 407 | |||||||||
Rated (nameplate) Cos-Phi of the motor. | ||||||||||||||||||||
P4-08 | Motor Autotune Mode | N/A | 0: Disabled / Auto-tune completed | 0 ... 4 | RO | N | N/A | 1 | 2198h | 0 | 408 | |||||||||
If an Autotune fails, the drive will trip and indicate an Autotune failed code, see | ||||||||||||||||||||
P4-09 | V/F Mode Voltage Boost | % | 0.0 % | 0.0...100.0 % | RW | Y | 1 = 0.1% | 1 | 2199h | 0 | 409 | |||||||||
Voltage boost is used to increase the applied motor voltage at low output frequencies, this can help improve low speed and starting torque. NoteNote : P4-01 is set to 1 or 2 then this parameter should be set to 0. | ||||||||||||||||||||
P4-10 | V/F Characteristic Adjustment Frequency | % | 0.0 | 0.0 to 100.0 | RW | Y | 1 = 0.1% | 2 | 219Ah | 0 | 410 | |||||||||
When operating in V/F mode (P4-01 = 2), this parameter in conjunction with P4-11 sets a frequency point (as a % of P4-04) at which the voltage set in P4-11 (as a % of P4-02) is applied to the motor. Care must be taken to avoid overheating and damaging the motor when using this feature. | ||||||||||||||||||||
P4-11 | V/F Characteristic Adjustment Voltage | % | 0.0 | 0.0 to 100.0 | RW | Y | 1 = 0.1% | 2 | 219Bh | 0 | 411 | |||||||||
Used in conjunction with P4-10 | ||||||||||||||||||||
P4-12 | Low frequency torque boost current at start | % | 0.0 | 0.0 to 200.0 | RW | Y | 1 = 0.1% | 2 | 219Ch | 0 | 412 | |||||||||
Only effective when operating without an encoder. Allows a Boost current to be applied at start-up and low frequency (limit defined by P4-13), as a % of the motor rated current (P4-03). Injecting some additional current into the motor at low speed to ensure that rotor alignment is maintained and improving operation during starting and low speed with additional holding torque. | ||||||||||||||||||||
P4-13 | Low frequency Torque Boost current at start Frequency limit | % | 0.0 | 0.0 to 100.0 | RW | Y | 1 = 0.1% | 2 | 219Dh | 0 | 413 | |||||||||
Frequency range for applied boost current (P4-12) as a % of motor rated frequency (P4-04). This sets the frequency cut-off point above which boost current (P4-120 is no longer applied to the motor. | ||||||||||||||||||||
P4-14 | Low frequency Torque boost current at stop | % | 0.0 | 0.0 to 200.0 | RW | Y | 1 = 0.1% | 2 | 219Eh | 0 | 414 | |||||||||
Only effective when operating without an encoder. Allows a Boost current to be applied at stop and low frequency (limit defined by P4-15), as a % of the motor rated current (P4-03). Injecting some additional current into the motor at low speed to ensure that rotor alignment is maintained and improving operation during stopping with additional holding torque. | ||||||||||||||||||||
P4-15 | Torque Boost Frequency limit at stop | % | 0.0 | 0.0 to 100.0 | RW | Y | 1 = 0.1% | 2 | 219Fh | 0 | 415 | |||||||||
Only effective when operating without an encoder. Frequency range for applied boost current (P4-14) as a % of motor rated frequency (P4-04). This sets the frequency cut-off point below which boost current is no longer applied to the motor. | ||||||||||||||||||||
P4-16 | Flux Braking Current Level | % | 0.0 | 0.0 to 200.0 | RW | Y | 1 = 0.1% | 2 | 21A0h | 0 | 416 | |||||||||
Additional flux during braking/regen | ||||||||||||||||||||
P4-17 | Torque Reduction time during stopping | sec | 1.0 | 0.0 to 10.0 | RW | Y | 1 = 0.1 s | 1 | 21A1h | 0 | 417 | |||||||||
Setting 0 means function is disabled. This parameter helps in reducing the noise in the lift car when the motor brake is applied due to the immediate removal of current. Increasing this value reduces audible noise, setting too high can result in reduced torque and rollback during stopping. | ||||||||||||||||||||
P4-18 | Maximum Motoring Torque Limit | % | 200.0 | 0.0 to 400.0 | RW | Y | 1 = 0.1% | 2 | 21A2h | 0 | 418 | |||||||||
When operating in Vector Speed motor control modes (P4-01 = 0, 1, 3), this parameter defines the maximum torque limit. | ||||||||||||||||||||
P4-19 | Maximum Regenerating Torque Limit | % | 150.0 | 0.0 to 400.0 | RW | Y | 1 = 0.1% | 2 | 21A3h | 0 | 419 | |||||||||
Active only in Vector Speed motor control modes. Sets the maximum regenerating torque allowed by the drive. | ||||||||||||||||||||
P4-20 | Slip Compensation Gain in Motoring mode | % | 100.0 | 0.0 to 400.0 | RW | Y | 1 = 0.1% | 2 | 21A4h | 0 | 420 | |||||||||
P4-21 | Slip Compensation Gain in Regenerating mode | % | 100.0 | 0.0 to 400.0 | RW | Y | 1 = 0.1% | 2 | 21A5h | 0 | 421 | |||||||||
P4-23 | Motor Thermistor Trip Reaction | N/A | 0: Stop at Next stop command and show thermistor fault message | 0 to 2 | RW | Y | N/A | 1 | 21A7h | 0 | 423 | |||||||||
| ||||||||||||||||||||
P4-24 | Motor Stator Resistance (Rs) | ohms | Rating Dependent | 0.000 ... 31.500 Ω | RW | N | 1 = 0.001 Ω | 2 | 21A8h | 0 | 424 | |||||||||
For Geared (Induction) and PM motors: phase to phase stator resistance value in ohms as measured following an Auto-tune. | ||||||||||||||||||||
P4-25 | Motor Rotor Resistance (Rr) | ohms | Rating Dependent | 0.000 ... 31.500 Ω | RW | N | 1 = 0.001 Ω | 2 | 21A9h | 0 | 425 | |||||||||
For Geared (Induction) motors: phase to phase rotor resistance value in ohms as measured following an Auto-tune. | ||||||||||||||||||||
P4-26 | Motor Stator Inductance (Lsd) | mH | Rating Dependent | 0.0 ... 6553.5 mH | RW | N | 1 = 0.1 mH | 2 | 21AAh | 0 | 426 | |||||||||
For Geared (Induction) motors: phase stator inductance value. For Gearless (Permanent Magnet) motors: phase d-axis stator inductance in Milli Henry (mH). | ||||||||||||||||||||
P4-27 | PM Motor stator inductance (Lsq) | mH | Rating Dependent | 0.0 ... 6553.5 mH | RW | N | 1 = 0.1 mH | 2 | 21ABh | 0 | 427 | |||||||||
P4-28 | Motor Magnetising current (Id rms) | Amps | Rating Dependent | 0.0 ... 10.5 A | RW | N | 1 = 0.1 A | 1 | 21ACh | 0 | 428 | |||||||||
For Geared (Induction) motors only: magnetizing / no load current, before Auto-tune, | ||||||||||||||||||||
P4-29 | Enhanced Generator Control Enable | N/A | 0: Disabled | 0 to 1 | RW | N | N/A | 1 | 21ADh | 0 | 429 | |||||||||
| ||||||||||||||||||||
P4-30 | Motor Magnetising Time | ms | 0 | 0 to 65535 | RW | N | N/A | 2 | 21AEh | 0 | 430 | |||||||||
Group 5 Motor Brake Control - Parameter List
Parameter Number | Parameter Name | Units | Default | Available Settings | Access | Change During Run | Scaling | Size (Bytes) | CAN Register | CAN Sub Index | Modbus Register | |||||||
---|---|---|---|---|---|---|---|---|---|---|---|---|---|---|---|---|---|---|
P5-01 | Brake Release Time | sec | 0.2 s | 0.0...5.0 s | RW | Y | 1 = 0.1 s | 1 | 21F5h | 0 | 501 | |||||||
Sets the delay time, following the contactor Delay time (P3-01) in which it takes for the motor brake to be released (Relay 2) and then drive output frequency ramps up. | ||||||||||||||||||
P5-02 | Brake Apply Delay | sec | 0.2 | 0.0 to 5.0 | RW | Y | 1 = 0.1 s | 1 | 21F6h | 0 | 502 | |||||||
Sets the delay time, for the motor brake to apply (Relay 2 to open). | ||||||||||||||||||
P5-03 | Brake Apply Speed | Hz rpm ft/s m/s | 0.00 0.00 0.00 0.00 | 0.00 to P8-01 | RW | Y | 1 = 0.01Hz 1 = 1 rpm | 2 | 21F7h | 0 | 503 | |||||||
Sets the delay time, following the contactor Delay time (P3-01) in which it takes for the motor brake to be released (Relay 2) and then drive output frequency ramps up. | ||||||||||||||||||
P5-04 | Brake Release Monitoring Enable | N/A | 0: Function Off | 0: Function Off to 2: Function Enabled | RW | Y | N/A | 1 | 21F8h | 0 | 504 | |||||||
| ||||||||||||||||||
P5-05 | Brake Release Monitoring Time | sec | 0.5 | 0.1 to 5.0 | RW | Y | 1 = 0.1 s | 1 | 21F9h | 0 | 505 | |||||||
If the monitoring terminal has not changed state in this time (since the brake has been released by relay 2 of the drive) then the drive will trip “bF-Err" or “bF-LoC" (if number of attempts as set in P5-06 has been met) | ||||||||||||||||||
P5-06 | Brake Release Number of Errors Before Lockout | N/A | 0 | 0 to 5 | RW | Y | N/A | 1 | 21FAh | 0 | 506 | |||||||
The drive will automatically try to clear the “bF-Err” at 1.5 second intervals for the number of times set, after each attempt the travel sequence will restart, once the number of brake release monitoring errors has reached the number set in this parameter a permanent trip "bF-LoC" will be displayed. | ||||||||||||||||||
P5-07 | Brake Release Monitoring Errors | N/A | 0 | 0 | RO | N | N/A | 2 | 21FBh | 0 | 507 | |||||||
Total number of “bF-Err" trips since the drive was installed. |
Group 6 Encoder - Parameter List
Parameter Number | Parameter Name | Units | Default | Available Settings | Access | Change During Run | Scaling | Size (Bytes) | CAN Register | CAN Sub Index | Modbus Register | |||||||||||||||||||||||||
---|---|---|---|---|---|---|---|---|---|---|---|---|---|---|---|---|---|---|---|---|---|---|---|---|---|---|---|---|---|---|---|---|---|---|---|---|
P6-02 | Encoder Feedback Direction | N/A | 0 : Clockwise Direction | 0 : Clockwise Direction 1 : Anti-Clockwise Direction | RW | N | N/A | 1 | 2259h | 0 | 602 | |||||||||||||||||||||||||
Changes the direction of the incremental signals of the encoder feedback signal.
| ||||||||||||||||||||||||||||||||||||
P6-03 | Encoder Pulses Per Revolution | N/A | 2048 | 256 ... 65535 | RW | N | N/A | 2 | 225Ah | 0 | 603 | |||||||||||||||||||||||||
Sets the number of Pulses Per Revolution for the encoder according the Encoder nameplate/datasheet. This value must be set correctly to guarantee proper operation of the drive when Encoder feedback mode is enabled (P6-05 >0). Typically values for Incremental encoders are 512, 1024, 2048, 4096 NoteWith an EnDat type encoder the drive reads from the encoder and populates this parameter value automatically. | ||||||||||||||||||||||||||||||||||||
P6-04 | Encoder Type | N/A | 0: None | See Table | RW | N | N/A | 1 | 225Bh | 0 | 604 | |||||||||||||||||||||||||
NoteFor settings 6,7,9,10 where a single ended encoder is used (e.g. A and B) the unused channels of the encoder module must be connected to 0V. | ||||||||||||||||||||||||||||||||||||
P6-05 | Encoder Feedback Enable | N/A | 0 : Encoder Feedback Disabled | 0 : Encoder Feedback Disabled 1 : Encoder Feedback Enabled | RW | N | N/A | 1 | 225Ch | 0 | 605 | |||||||||||||||||||||||||
Enables or disables encoder feedback. When the encoder is disabled referred to as open loop and when the encoder is enabled it is referred to as closed loop.
NoteEven if P6-05 is set to 0 (Encoder Feedback Disabled) encoder feedback can still be monitored (P0-19) providing P6-03 and P6-04 have been set correctly. Encoder feedback Errors are disabled in this mode of operation. | ||||||||||||||||||||||||||||||||||||
P6-06 | Encoder Feedback Filter at Start | ms | 4 | 0 ... 20 | RW | Y | 1 = 1 ms | 1 | 225Dh | 0 | 606 | |||||||||||||||||||||||||
Helps in situations where there is noise on the Incremental encoder cables, and also allows for setting of higher speed loop gains. | ||||||||||||||||||||||||||||||||||||
P6-07 | Encoder Feedback Filter Whilst Running | ms | 4 | 0 ... 20 | RW | Y | 1 = 1 ms | 1 | 225Eh | 0 | 607 | |||||||||||||||||||||||||
Helps in situations where there is noise on the Incremental encoder cables, and also allows for setting of higher speed loop gains. | ||||||||||||||||||||||||||||||||||||
P6-08 | Encoder Feedback Filter at Stop | ms | 4 | 0 ... 20 | RW | Y | 1 = 1 ms | 1 | 225Fh | 0 | 608 | |||||||||||||||||||||||||
Helps in situations where there is noise on the Incremental encoder cables, and also allows for setting of higher speed loop gains. | ||||||||||||||||||||||||||||||||||||
P6-09 | Encoder Offset | deg | 0.0 | 0.0 ... 359.9 | RW | N | 1 = 0.1 deg | 2 | 2260h | 0 | 609 | |||||||||||||||||||||||||
As measured by the stationary encoder offset measurement Value will be wrong if the motor poles (P4-05) has been set incorrectly or if an Encoder offset measurement has not been performed. | ||||||||||||||||||||||||||||||||||||
P6-10 | Encoder Count/Position | deg | 0.0 | 0.0 ... 359.9 | RO | N | 1 = 0.1 deg | 2 | 2261h | 0 | 610 | |||||||||||||||||||||||||
Real-time position of the encoder. | ||||||||||||||||||||||||||||||||||||
P6-11 | Speed Error Trip Level | % | 10.0 | 0.0 ... 100.0 | RW | Y | 1 = 0.1% | 2 | 2262h | 0 | 611 | |||||||||||||||||||||||||
This parameter defines the maximum permissible speed error between the encoder feedback speed value and the estimated rotor speed calculated by the motor control algorithms. If the speed error exceeds this limit (for the time set in Parameter P6-12 Speed Error Trip Detection Time) , the drive will trip SP-Err. When set to zero, this protection is disabled. Active with and without an Encoder (P6-05 = 0 or 1 | ||||||||||||||||||||||||||||||||||||
P6-12 | Speed Error Trip Detection Time | sec | 0.1 | 0.0 ... 5.0 | RW | Y | 1 = 0.1 | 1 | 2263h | 0 | 612 | |||||||||||||||||||||||||
Used in Conjunction with P6-11 (Speed Error Trip Level) | ||||||||||||||||||||||||||||||||||||
P6-13 | Encoder Module Error Code | N/A | 0 | RO | N | N/A | 1 | 2264h | 0 | 613 | ||||||||||||||||||||||||||
Displays Error for Universal Encoder Module. | ||||||||||||||||||||||||||||||||||||
P6-14 | Encoder Comms signal Quality | % | 0% | 0.00 ... 100.00 % | RO | N | 1 = 0.1% | 2 | 2265h | 0 | 614 | |||||||||||||||||||||||||
Displays Communication Signal quality. |
Group 7 Rescue Operation - Parameter List
Parameter Number | Parameter Name | Units | Default | Available Settings | Access | Change During Run | Scaling | Size (Bytes) | CAN Register | CAN Sub Index | Modbus Register | |||||||
---|---|---|---|---|---|---|---|---|---|---|---|---|---|---|---|---|---|---|
P7-01 | Rescue Supply type | N/A | 0 : 230V UPS | 0 : 230V UPS 1 : 400V UPS 2 : Battery Operation | RW | N | N/A | 1 | 22BDh | 0 | 701 | |||||||
Select what type of power supply is being used for Rescue Mode Operation
| ||||||||||||||||||
P7-02 | Rescue Operation Function | N/A | 0: Basic Rescue Mode | 0 : Basic Rescue Mode 1 : Light Load Detection 2 : UPS Easiest Direction based on Load Measurement 3 : Energy Optimized | RW | N | N/A | 1 | 22BEh | 0 | 702 | |||||||
There are 3 types of rescue mode operation, the following points of consideration help select the most suitable mode:
| ||||||||||||||||||
P7-03 | Rescue Mode Speed | Hz / rpm / ft/s / m/s | 5.00 Hz | P8-02 ... P8-01 | RW | Y *Does not take effect until next travel | 1 = 0.1 Hz | 2 | 22BFh | 0 | 703 | |||||||
This parameter defines the motor speed during rescue mode operation (when Rescue mode Input is activated), the value is also controlled internally by the power limit function based on the UPS rating entered into parameter P7-04. The actual achievable speed will be limited depending on a number of factors such as DC bus voltage level, motor, travel speed, system efficiencies, estimated value can be calculated as follows : It should also be noted that the level of motor load will affect the available DC bus Voltage; in some cases it may be necessary to reduce the Rescue Speed further in order to prevent nuisance Under Voltage (“U-volt”) trips. | ||||||||||||||||||
P7-04 | UPS Rating | kW | 0.0 | 0.0 ... 65535 | RW | Y | 1 = 0.1 kW | 2 | 22C0h | 0 | 704 | |||||||
Used to protect overloading/ collapsing of voltage of the UPS power supply which could cause a motor stall condition. When the output power to the motor exceeds this value for the time set in parameter (P7-16) UPS Overload Time Limit, the drive will ramp down to Stop, apply brakes (if controlled by the drive) and trip on “UPS-L”, to restart a new direction command will need to be provided by the controller. If value is set to 0.0 then this function is disabled. | ||||||||||||||||||
P7-05 | Rescue Mode Current Limit | % | 100.0% | 0.0 ... 200.0% | RW | Y | 1 = 0.1% | 2 | 22C1h | 0 | 705 | |||||||
Set the current limit during rescue mode operation. | ||||||||||||||||||
P7-06 | Rescue Mode Proportional Speed Loop Gain | % | 10.0% | 0.0 ...400.0% | RW | Y | 1 = 0.1% | 2 | 22C2h | 0 | 706 | |||||||
Sets the Rescue Mode P-Gain to improve speed stability during rescue operation. | ||||||||||||||||||
P7-07 | Rescue Mode Integral Speed Loop Gain | ms | 50ms | 0 ...1000ms | RW | Y | 1 = 0.1ms | 2 | 22C3h | 0 | 707 | |||||||
Sets the Rescue Mode I-Gain to improve speed stability during rescue operation. | ||||||||||||||||||
P7-08 | Light Load Detection Measurement time | sec | 1.0s | 0.0 ...10.0s | RW | Y | 1 = 0.1s | 1 | 22C4h | 0 | 708 | |||||||
This parameter determines the time in which the light load detection function runs at the speed set in P7-10 (Light Load Speed Detection Speed) in each direction. | ||||||||||||||||||
P7-09 | Light Load Detection Speed | Hz / rpm / ft/s / m/s | 5.00 | P8-02 ... P8-01 | RW | Y *Does not take effect until next travel | 1 = 0.01Hz 1 = 1rpm | 2 | 22C5h | 0 | 709 | |||||||
This parameter determines the motor speed during the Light Load Detection test in each direction. | ||||||||||||||||||
P7-10 | Load Measurement extended time | sec | 0.0s | 0.0 ...10.0s | RW | Y | 1 = 0.1s | 1 | 22C6h | 0 | 710 | |||||||
Increasing this value can help improve the measurement accuracy of the UPS Easiest Direction based on measurement function. | ||||||||||||||||||
P7-11 | Light Load Detection Results | N/A | 0: Light direction is clockwise | 0 : Light direction is clockwise 1 : Light direction is Anti-clockwise 2 : Balanced | RO | N | N/A | 1 | 22C7h | 0 | 711 | |||||||
This parameter shows the result of the Rescue Mode function tests when P7-02=1 or P7-02 =2.
| ||||||||||||||||||
P7-12 | Energy Saving Rescue Unbalancing Max speed | Hz / rpm / ft/s / m/s | 5.00 Hz | P8-02...P8-01 | RW | Y | 1 = 0.01Hz | 2 | 22C8h | 0 | 712 | |||||||
P7-13 | Energy Saving Rescue Minimum Speed | Hz / rpm / ft/s / m/s | 5.00 Hz | P8-02...P8-01 | RW | Y | 1 = 0.01Hz | 2 | 22C9h | 0 | 713 | |||||||
P7-14 | Energy Saving Rescue Minimum Speed Time | sec | 0.0s | 0.0 ...10.0s | RW | Y | 1 = 0.1s | 1 | 22CAh | 0 | 714 | |||||||
P7-15 | Rescue mode active | N/A | 0 : Mains Supply | 0 : Mains Supply 1 : Rescue Supply | RO | N | N/A | 1 | 22CBh | 0 | 715 | |||||||
Displays the active supply that the drive is being operated from.
| ||||||||||||||||||
P7-16 | UPS overload time limit | sec | 2.0s | 0.0 ...10.0s | RW | N | 1 = 0.1s | 1 | 22CCh | 0 | 716 | |||||||
Used in conjunction with parameter P7-04 (UPS rating). When the value in P7-04 is exceeded for the cumulative time set in this parameter the drive will trip UPS-L. NoteIf P7-04 is 0 UPS Protection is disabled and the time in this parameter is not used. |
Group 8 Travel Curve - Parameter List
Parameter Number | Parameter Name | Units | Default | Setting Range | Access | Change During Run | Scaling | Size (Bytes) | CAN Register | CAN Sub Index | Modbus Register |
---|---|---|---|---|---|---|---|---|---|---|---|
P8-01 | Maximum Frequency / Speed Limit | Hz / rpm / ft/s / m/s | 50.00 | P8-02 to 500.00 Hz | RW | N | 1 = 0.01Hz | 2 | 2321h | 0 | 801 |
Maximum output motor speed limit. If P4-06 (motor rated speed) >0, the value entered / displayed is in Rpm. If System information has been entered into P3-08 (sheave diameter), P3-09 (roping ratio), P3-10(Gear ratio) then value entered/displayed will be in linear units. This parameter is updated automatically to match the values set in the motor rated frequency (P4-04) and motor rated speed (P4-06), the user can also set the value independently. | |||||||||||
P8-02 | Minimum Frequency/Speed Limit | Hz / rpm / ft/s / m/s | 0.00 | 0.00 to P8-01 | RW | N | 1 = 0.01Hz | 2 | 2322h | 0 | 802 |
Minimum motor speed limit. | |||||||||||
P8-03 | Acceleration ramp time | sec | 2.00 | 0.00 to 600.00 | RW | Y | 1 = 0.1 | 2 | 2323h | 0 | 803 |
Ramp used when accelerating to a speed. Jerks used P9-01 and P9-02. | |||||||||||
P8-04 | Deceleration ramp time | sec | 2.00 | 0.00 to 600.00 | RW | Y | 1 = 0.1 | 2 | 2324h | 0 | 804 |
Ramp used when decelerating to a speed reference >0. | |||||||||||
P8-05 | Levelling Speed | Hz / rpm / ft/s / m/s | 5.00 | P8-02 to P8-01 | RW | Y | 1 = 0.01Hz | 2 | 2325h | 0 | 805 |
P8-06 | High Speed | Hz / rpm / ft/s / m/s | 50.00 | P8-02 to P8-01 | RW | Y | 0.01 = 1Hz | 2 | 2326h | 0 | 806 |
P8-07 | Intermediate Speed | Hz / rpm / ft/s / m/s | 25.00 | P8-02 to P8-01 | RW | Y | 0.01 = 1Hz | 2 | 2327h | 0 | 807 |
P8-08 | Inspection Speed | Hz / rpm / ft/s / m/s | 5.00 | P8-02 to P8-01 | RW | Y | 0.01 = 1Hz | 2 | 2328h | 0 | 808 |
P8-09 | High Speed 2 | Hz / rpm / ft/s / m/s | 0.00 | P8-02 to P8-01 | RW | Y | 0.01 = 1Hz | 2 | 2329h | 0 | 809 |
P8-10 | High Speed 3 | Hz / rpm / ft/s / m/s | 0.00 | P8-02 to P8-01 | RW | Y | 0.01 = 1Hz | 2 | 232Ah | 0 | 810 |
P8-11 | High Speed 4 | Hz / rpm / ft/s / m/s | 0.00 | P8-02 to P8-01 | RW | Y | 0.01 = 1Hz | 2 | 232Bh | 0 | 811 |
P8-12 | High Speed 5 / Re-levelling Speed | Hz / rpm / ft/s / m/s | 0.00 | P8-02 to P8-01 | RW | Y | 0.01 = 1Hz | 2 | 232Ch | 0 | 812 |
P8-13 | Action on Zero Reference | N/A | 0 : Direction removed | 0 : Direction removed 1 : Direction removed or zero speed reference | RW | N | N/A | 1 | 232Dh | 0 | 813 |
When set to 0 the stopping condition is direction command removed. If a zero speed reference is given the drive will stay enabled at zero until the direction command is removed. When set to 0 the stopping condition is direction command removed. If a zero speed reference is given the drive will stay enabled at zero until the direction command is removed. |
Group 9 Comfort Optimisation - Parameter List
Parameter Number | Parameter Name | Units | Default | Available Settings | Access | Change Run | Scaling | Size (Bytes) | CAN Register | CAN Sub Index | Modbus Register |
---|---|---|---|---|---|---|---|---|---|---|---|
P9-01 | Acceleration Start Jerk | sec | 1.0 | 0.0 ... 5.0 | RW | Y | 1 = 0.01 s | 2 | 2385h | 0 | 901 |
P9-02 | Acceleration End Jerk | sec | 1.0 | 0.0 ... 5.0 | RW | Y | 1 = 0.01 s | 2 | 2386h | 0 | 902 |
P9-03 | Deceleration Start Jerk | sec | 1.0 | 0.0 ... 5.0 | RW | Y | 1 = 0.01 s | 2 | 2387h | 0 | 903 |
P9-04 | Deceleration End Jerk | sec | 1.0 | 0.0 ... 5.0 | RW | Y | 1 = 0.01 s | 2 | 2388h | 0 | 904 |
P9-05 | Levelling End Jerk | sec | 1.0 | 0.0 ... 5.0 | RW | Y | 1 = 0.01 s | 2 | 2389h | 0 | 905 |
P9-06 | Stopping Ramp Time | sec | 0.0 | 0.0 ... 5.0 | RW | Y | 1 = 0.01 s | 2 | 238Ah | 0 | 906 |
P9-07 | Stopping Jerk | sec | 1.0 | 0.0 ... 5.0 | RW | Y | 1 = 0.01 s | 2 | 238Bh | 0 | 907 |
P9-08 | Smooth Start Time | sec | 0.0 | 0.0 ... 5.0 | RW | Y | 1 = 0.1 s | 1 | 238Ch | 0 | 908 |
P9-09 | Smooth Start Speed | Hz / rpm / ft/s / m/s | 5.00 | 0.00 ... 1.00 Hz | RW | Y | 1 = 0.01Hz | 2 | 238Dh | 0 | 909 |
P9-10 | Smooth Start Ramp Time | sec | 0.50 | 600.00 | RW | Y | 1 = 0.01 s | 2 | 238Eh | 0 | 910 |
P9-11 | DC Injection Time At Start | sec | 0.5 | 0.0 to 10.0 | RW | Y | 1 = 0.1 s | 1 | 238Fh | 0 | 911 |
Helps eliminate starting rollback in geared open loop applications. Function Disabled if value entered = 0.0. Best value is the shortest time but with the least amount of rollback. | |||||||||||
P9-12 | DC Injection Current At Start | % | 50 | 0.0 to 200.0 | RW | Y | 1 = 0.1 % | 2 | 2390h | 0 | 912 |
Helps eliminate starting rollback in geared open loop applications. Function Disabled if value entered = 0.0. Best value is the lowest value but with the least amount of rollback, the higher the value the more heat generated in the motor. | |||||||||||
P9-13 | Position Lock / DC Injection Time At Stop | sec | 0.5 | 0.0 to 10.0 | RW | Y | 1 = 0.1 s | 1 | 2391h | 0 | 913 |
Helps eliminate stopping rollback in geared open loop applications. Function Disabled if value entered = 0.0. Best value is the shortest time but with the least amount of rollback. | |||||||||||
P9-14 | DC Injection Current At Stop | % | 50.0 | 0.0 to 200.0 | RW | Y | 1 = 0.1 % | 2 | 2392h | 0 | 914 |
Helps eliminate stopping rollback in geared open loop applications. Function Disabled if value entered = 0.0. Best value is the lowest value but with the least amount of rollback, the higher the value the more heat generated in the motor and nuisance over current trips. | |||||||||||
P9-15 | Position Lock / DC Injection Speed At Stop | Hz / rpm / ft/s / m/s | 0.0 | 0.0 to P8-01 | RW | Y | 1 = 0.01Hz 1 = 1rpm | 2 | 2393h | 0 | 915 |
Helps eliminate stopping rollback in geared open loop applications. DC Injection function is disabled if value entered = 0.0. Best to aim for the lowest suitable value, as too high a value can cause the motor to stop to early resulting in the lift car stopping before reaching the floor. | |||||||||||
P9-16 | Rollback Control P-gain at Start | % | 0.0 | 0.0 to 400.0 | RW | Y | 1 = 0.1 % | 2 | 2394h | 0 | 916 |
P9-18 | Rollback Control Activation Pulses | 4PPR | 10 | 0 to 10 | RW | Y | N/A | 1 | 2396h | 0 | 918 |
This parameter determines the number of measured encoder feedback pulses before the Rollback Control gain parameters activate. | |||||||||||
P9-22 | Zero Speed Holding Time on Disable | sec | 0.2 | 0.0 to 100.0 | RW | Y | 1 = 0.1 s | 2 | 239Ah | 0 | 922 |
Sets the zero speed holding time, between reaching the DC Injection speed at Stop P9-15 and the brake command being given to engage the brake | |||||||||||
P9-23 | Speed Loop Proportional Gain at Start | 50% | 50.0 | 0.0 to 400.0 | RW | Y | 1 = 0.1 % | 2 | 239Bh | 0 | 923 |
P9-24 | Speed Loop Integral Gain at Start | ms | 50 | 0 to 1000 | RW | Y | 1 = 1 ms | 2 | 239Ch | 0 | 924 |
P9-25 | Speed Loop Gain Transition Speed During Acceleration | Hz / rpm / ft/s / m/s | 0.00 | 0.0 to P8-01 | RW | Y | 1 = 0.01Hz | 2 | 239Dh | 0 | 925 |
P9-26 | Speed Loop Gain Transition Bandwidth During Acceleration | Hz / rpm / ft/s / m/s | 0.00 | 0.0 to P8-01 | RW | Y | 1 = 0.01Hz | 2 | 239Eh | 0 | 926 |
P9-27 | Speed Loop Proportional Gain During Run | % | 50 | 0 to 400 | RW | Y | 1 = 0.1 % | 2 | 239Fh | 0 | 927 |
P9-28 | Speed Loop Integral Gain During Run | ms | 50 | 0 to 1000 | RW | Y | 1 = 1 ms | 2 | 23A0h | 0 | 928 |
P9-29 | Speed Loop Differential Gain During Run | % | 0.0 | 0.0 to 400.0 | RW | Y | 1 = 0.1 % | 2 | 23A1h | 0 | 929 |
P9-30 | Speed Loop Proportional Gain During Deceleration | % | 50 | 0 to 400 | RW | Y | 1 = 0.1 % | 2 | 23A2h | 0 | 930 |
P9-31 | Speed Loop Integral Gain During Deceleration | ms | 50 | 0 to 1000 | RW | Y | 1 = 1 ms | 2 | 23A3h | 0 | 931 |
P9-32 | Speed Loop Gain Transition Speed During Deceleration | Hz / rpm / ft/s / m/s | 0.00 | 0.0 to P8-01 | RW | Y | 1 = 0.01Hz | 2 | 23A4h | 0 | 932 |
P9-33 | Speed Loop Gain Transition Bandwidth During Deceleration | Hz / rpm / ft/s / m/s | 0.00 | 0.0 to P8-01 | RW | Y | 1 = 0.01Hz | 2 | 23A5h | 0 | 933 |
P9-34 | Speed Loop Proportional Gain at Zero Speed | % | 50 | 0 to 400 | RW | Y | 1 = 0.1 % | 2 | 23A6h | 0 | 934 |
P9-35 | Speed Loop Integral Gain at Zero Speed | ms | 50 | 0 to 1000 | RW | Y | 1 = 1 ms | 2 | 23A7h | 0 | 935 |
P9-36 | Motor Pre-Torque in Clockwise Direction | % | 0.0 | -100 to 100 | RW | Y | 1 = 0.1 % | 2 | 23A8h | 0 | 936 |
P9-37 | Motor Pre-Torque in Counter-Clockwise Direction | % | 0.0 | -100 to 100 | RW | Y | 1 = 0.1 % | 2 | 23A9h | 0 | 937 |
P9-38 | Speed Error Dead Band | % | 2.0 | 0.0 to 100.0 | RW | Y | 1 = 0.1 % | 2 | 23AAh | 0 | 938 |
Group 10 Extended Functions - Parameter List
Parameter Number | Parameter Name | Units | Default | Available Settings | Access | Change Run | Scaling | Size (Bytes) | CAN Register | CAN Sub Index | Modbus Register | |||||
---|---|---|---|---|---|---|---|---|---|---|---|---|---|---|---|---|
P10-01 | Enable Short Floor Operation | N/A | 0: Disabled | 0 : Disabled 1 : Enabled | RW | N | N/A | 1 | 23E9h | 0 | 1001 | |||||
Enables Short Floor Operation | ||||||||||||||||
P10-02 | Early Door Opening Speed Threshold | % | 0.0 | 0.0 ... 100.0 | RW | Y | 1 = 0.1 % | 2 | 23EAh | 0 | 1002 | |||||
Any of the drives digital outputs or relays can be set to give an output when the door zone speed condition has been met (setting 16), example of using Digital output 3 shown above. The output will only come on during deceleration approaching the floor. | ||||||||||||||||
P10-03 | Travel Direction Change Counter (non-resettable) | N/A | 0 | 0 ... 4294967295 | RO | N | N/A | 4 | 23EBh | 0 | 1003 | |||||
Counts up by 1 every time there is a change in travel direction. | ||||||||||||||||
P10-04 | Travel Direction Change Counter | N/A | 0 | 0 ... 4294967295 | RO | N | N/A | 4 | 23ECh | 0 | 1004 | |||||
Counts up by 1 every time there is a change in travel direction. | ||||||||||||||||
P10-05 | Travel Direction Change Counter limit | N/A | 0 | 0 ... 4294967295 | RW | Y | N/A | 4 | 23EDh | 0 | 1005 | |||||
When the value entered in this parameter has been reached a warning message (tr-Lt) is shown on the drive display and a digital output or Relay will come on (If output source is set for 18 - Travel Limit Counter Reached - example of using Digital output 3 shown above). | ||||||||||||||||
P10-06 | Reset motor direction change counter | N/A | 0 : Disabled | 0 : Disabled 1 : Reset | RW | Y | N/A | 1 | 23EEh | 0 | 1006 | |||||
| ||||||||||||||||
P10-07 | Number of travels | N/A | 0 | 0 ... 4294967295 | RO | N | N/A | 4 | 23EFh | 0 | 1007 | |||||
Counts up by 1 on every drive enable signal given. | ||||||||||||||||
P10-08 | Motor Connected Check | % | 5.0 | 0.0 ... 100.0 | RW | N | 1 = 0.1 % | 2 | 23F0h | 0 | 1008 | |||||
To ensure that the motor is connected, the drive has a function which checks that at each start command all 3 phases of the motor are connected prior to releasing the electro-mechanical brake. This function checks for breaks in the connection between the drive and the motor, for example a broken cable or a faulty contactor. The drive will trip “OUt-Phx” if the drive detects the motor is not connected, where x is the phase that is missing e.g. "OUt-phU" Setting 0.0 means function is disabled. | ||||||||||||||||
P10-09 | Anti-Stall | N/A | 0 : Disabled | 0 :Disabled 1 : Enabled | RW | N | N/A | 1 | 23F1h | 0 | 1009 | |||||
| ||||||||||||||||
P10-10 | Anti-Stall Limit | % | 100.0% | 100.0 ... 250.0% | RW | N | 1 = 0.1 % | 2 | 23F2h | 0 | 1010 | |||||
Set as a % of motor rated current | ||||||||||||||||
P10-11 | Anti-Stall Hysteresis | % | 10.0% | 0.0 ... 50.0% | RW | N | 1 = 0.1 % | 2 | 23F3h | 0 | 1011 | |||||
Set as a % of motor rated current | ||||||||||||||||
P10-12 | Overspeed Governor test speed | 23F4h | 0 | 1012 | ||||||||||||
Once a value of >0.0 has been entered, the next run command from the controller to the drive will result in the motor running at the value set in terms of a % of the value set in the High-Speed parameter (P8-06), then at the next stop command the value of the parameter will return to 0.0 automatically so that the test is not repeated, and normal operation is resumed. | ||||||||||||||||
P10-13 | Travel Direction Change Counter Limit Reached | N/A | 0 | 0 ... 1 | RO | N | N/A | 1 | 23F5h | 0 | 1013 |
Group 11 Drive Configuration - Parameter List
Parameter Number | Parameter Name | Units | Default | Available Settings | Access | Change During Run | Scaling | Size (Bytes) | CAN Register | CAN Sub Index | Modbus Register | |||||||||||||||
---|---|---|---|---|---|---|---|---|---|---|---|---|---|---|---|---|---|---|---|---|---|---|---|---|---|---|
P11-01 | Save User Defaults | N/A | 0: No Action | See Table | RW | N | N/A | 1 | 244Dh | 0 | 1101 | |||||||||||||||
| ||||||||||||||||||||||||||
P11-02 | Extended Group Access Code | N/A | 0 | 0 ... 9999 | RW | Y | N/A | 2 | 244Eh | 0 | 1102 | |||||||||||||||
The value entered in parameter P11-02 determines which parameter groups are accessible by the user. By Default if :
Level 1 access includes groups 0 through to group 11. Level 2 access includes groups 0 through to group 12. The code for Level 2 can be changed by the user by setting the desired value into parameter P11-04 | ||||||||||||||||||||||||||
P11-03 | Parameter Access Lock | N/A | 0: Unlocked | 0 : Unlocked 1 : Locked | RW | Y | N/A | 1 | 244Fh | 0 | 1103 | |||||||||||||||
| ||||||||||||||||||||||||||
P11-04 | Level 2 Access Definition | N/A | 101 | 0 ... 9999 | RW | Y | N/A | 2 | 2450h | 0 | 1104 | |||||||||||||||
Enter your chosen access code here (>0) which once set must be entered in P11-02 to access parameter Group 2 Once set this parameter will become hidden until the same value is entered into P11-02 | ||||||||||||||||||||||||||
P11-05 | Effective Switching Frequency | kHz | 8.0 kHz | 2.0 ... 10.0 kHz | RW | N | 1 = 0.1 Hz | 1 | 2451h | 0 | 1105 | |||||||||||||||
IGBT Switching Frequency. Higher switching frequencies reduce the audible ‘ringing’ noise from the motor and improve the output current waveform at the expense of increased drive losses. | ||||||||||||||||||||||||||
P11-06 | Auto Thermal Management | kHz | 2.0 kHz | 2.0 ... 10.0 kHz | RW | N | 1 = 0.1 Hz | 1 | 2452h | 0 | 1106 | |||||||||||||||
This parameter defines the minimum effective switching frequency which the drive will use when the drive auto- switches down the switching frequency (Based on Heatsink Temperature and motor current) in order to reduce the losses and heat from the power stage. | ||||||||||||||||||||||||||
P11-07 | Thermal Overload Value Retention Enable | N/A | 0 : Disabled | 0 : Disabled 1 : Enabled | RW | N | N/A | 1 | 2453h | 0 | 1107 | |||||||||||||||
When P11-07 is 0, removing the power supply from the drive and re-applying will reset the value of the accumulator. When P11-07 is 1, the value is retained during power off.
| ||||||||||||||||||||||||||
P11-09 | Output Phase Sequence | N/A | 0 : U, V, W | 0 : U, V, W 1 : U, W, V | RW | N | N/A | 1 | 2455h | 0 | 1109 | |||||||||||||||
Select the motor phase orientation.
| ||||||||||||||||||||||||||
P11-10 | PWM Modulation Type | N/A | 0 : 3-Phase | 0 : 3-Phase 1 : 2-Phase 2 : Auto | RW | N | N/A | 1 | 2456h | 0 | 1110 | |||||||||||||||
Selects the type of PWM modulation.
| ||||||||||||||||||||||||||
P11-11 | Display Scaling Factor | N/A | 0.000 | -30.000 ... 30.000 | RW | Y | 1 = 0.001 | 2 | 2457h | 0 | 1111 | |||||||||||||||
P11-11 & P11-12 allow the user to program the drive to display an alternative output unit scaled from an existing parameter, e.g. to display speed in meters per second based on the output frequency. If P11-11 is set >0, the variable selected in P11-12 is multiplied by the factor entered in P11-11, and displayed whilst the drive is running with a ‘c’ to indicate the customer scaled units. NoteThis function is disabled if P11-11 is set to 0. | ||||||||||||||||||||||||||
P11-12 | Display Scaling Source | N/A | 2 | See Table | RW | Y | N/A | 1 | 2458h | 0 | 1112 | |||||||||||||||
Source to be multiplied by P11-11
| ||||||||||||||||||||||||||
P11-13 | Reset Cooling Fan Run-time | N/A | 0 : Disabled | 0 : Disabled 1 : Reset | RW | N | N/A | 1 | 2459h | 0 | 1113 | |||||||||||||||
Setting to 1 resets the internal Fan run-time counter to zero (as displayed in P0-65). | ||||||||||||||||||||||||||
P11-14 | Cooling Fan Control | N/A | 0 | See Table | RW | N | N/A | 1 | 245Ah | 0 | 1114 | |||||||||||||||
| ||||||||||||||||||||||||||
P11-15 | Cooling Fan Run-time After Disable | sec | 60 s | 0 ... 600 s | RW | N | N/A | 2 | 245Bh | 0 | 1115 | |||||||||||||||
This parameter defines the fan run time after disable if the drive is at the fan turn on temperature. | ||||||||||||||||||||||||||
P11-16 | Resets kWh Meter | N/A | 0 : Disabled | 0 : Disabled 1 : Reset | RW | N | N/A | 1 | 245Ch | 0 | 1116 | |||||||||||||||
Setting to 1 resets the internal energy consumption kWh meter to zero (as displayed in P13-57 and P13-58). | ||||||||||||||||||||||||||
P11-17 | Service time interval | hours | 0 h | 0 ... 65535 h | RW | N | 1 = 1 hour | 2 | 245Dh | 0 | 1117 | |||||||||||||||
This defines the total number of run time hours which must elapse before the Service indicator output comes on (e.g. DA1 Output 1 function select setting 14). NoteTo reset this value set P11-19 to 1. | ||||||||||||||||||||||||||
P11-18 | Time remaining to next service | hours | 0 h | -65536 ... 65535 h | RO | N | 1 = 1 hour | 2 | 245Eh | 0 | 1118 | |||||||||||||||
Displays the number of hours remaining on the service counter before the next service is due. A negative value shows the service overdue hours. | ||||||||||||||||||||||||||
P11-19 | Reset service time indicator | N/A | 0 : Disabled | 0 : Disabled 1 : Reset | RW | Y | N/A | 1 | 245Fh | 0 | 1119 | |||||||||||||||
When this parameter is set to 1, the internal Service time interval counter (P11-17) is reset. | ||||||||||||||||||||||||||
P11-20 | Motor Thermistor Trip Threshold | Ω | 2500 Ω | 0 ... 5000 Ω | RW | Y | 1 = 1 Ω | 2 | 2460h | 0 | 1120 | |||||||||||||||
Sets the trip threshold resistance for the connected motor thermistor. | ||||||||||||||||||||||||||
P11-21 | Motor Thermistor Reset Threshold | Ω | 1900 Ω | 0 ... 5000 Ω | RW | Y | 1 = 1 Ω | 2 | 2461h | 0 | 1121 | |||||||||||||||
Sets the trip reset threshold resistance for the connected motor thermistor. | ||||||||||||||||||||||||||
P11-22 | P0-75 Display Index | N/A | 0 | 0 ... 99999 | RW | Y | N/A | 2 | 2462h | 0 | 1122 | |||||||||||||||
Internal Use Only | ||||||||||||||||||||||||||
P11-23 | Disable Run Sequence Error Detection | N/A | 1: Disabled | 0 : Disabled 1 : Enabled | RW | Y | N/A | 1 | 2463h | 0 | 1123 | |||||||||||||||
This function checks that the control commands sent from the controller to the drive are in the following expected order. Expected Order:
| ||||||||||||||||||||||||||
P11-30 | Drive Type Code | N/A | Drive Dependent | RO | N | N/A | 2 | 246Ah | 0 | 1130 | ||||||||||||||||
P11-31 | Drive Branding Identifier | N/A | Drive Dependent | 0 ... 65535 | RO | N | N/A | 2 | 246Bh | 0 | 1131 | |||||||||||||||
P11-37 | Drive rated current | Amps | Drive Dependent | N/A | RO | N | 1 = 0.1A | 2 | 2471h | 0 | 1137 | |||||||||||||||
P11-38 | Drive rated voltage | Volts | Drive Dependent | N/A | RO | N | N/A | 2 | 2472h | 0 | 1138 | |||||||||||||||
P11-39 | Drive rated power (kW) | kW | Drive Dependent | N/A | RO | N | 1 = 0.1 kW | 2 | 2473h | 0 | 1139 | |||||||||||||||
P11-40 | Drive rated power (HP) | HP | Drive Dependent | N/A | RO | N | 1 = 0.1 HP | 2 | 2474h | 0 | 1140 | |||||||||||||||
P11-41 | Number of input phases | N/A | Drive Dependent | 1 ... 3 | RO | N | N/A | 1 | 2475h | 0 | 1141 | |||||||||||||||
P11-42 | Drive frame size | N/A | Drive Dependent | 1 ... 5 | RO | N | N/A | 1 | 2476h | 0 | 1142 | |||||||||||||||
P11-43 | Duty Rating | N/A | Drive Dependent | 0 ... 1 | RO | N | N/A | 1 | 2477h | 0 | 1143 | |||||||||||||||
P11-44 | IP Rating | N/A | Drive Dependent | 0 ... 66 | RO | N | N/A | 1 | 2478h | 0 | 1144 |
Rescue Mode with Battery Supply - Overview
Rescue operation is normally used in the event of a mains borne power failure, with the primary goal of moving the elevator car at a limited motor speed for passenger evacuation, the power source comes from either DC (Batteries) or a UPS power supply.
To setup Rescue Mode with a Battery Supply click Next or use the links below to find a specific section.
Functional differences in Rescue Mode
During Rescue Mode operation the following functions and trips are disabled/altered:
Function | Rescue Mode |
---|---|
Input Phase Loss Detection | Disabled |
DC bus Ripple detection | Disabled |
Undervoltage trip levels | Reduced - Exact values |
Speed Loop Gains - Group 9 | No Longer Active Rescue Mode has it's own dedicated gains in (P7-06 and P7-07) |
Motor Autotune | Disabled |
Speed Reference | Rescue mode speed is governed by value set in P7-03. To run the drive in Rescue Mode the Inputs: STO1/STO2 and a Direction command must be closed. |
Battery Supply Requirements
When operating in battery mode the drive uses a different set of conditions for operation voltage thresholds. These are detailed in the table below.
Supply Type | Minimum Voltage | Nominal Battery Voltage | Maximum Battery Voltage | Current Requirements |
---|---|---|---|---|
Main Voltage Input: +DC and -DC terminals Figure 1. DC Supply Connections Make sure the correct polarity of DC connections is made to the drive (+ to + / - to -). | 32Vdc (<24Vdc will result in an under-voltage trip) | 48Vdc | 230V Rated Drive 290Vdc 400V Rated Drive 510Vdc | No less than the value of the Motor Rated current nameplate value and considering overload, typically no greater than 200% |
Control Voltage Input Red = +24V Black = 0Vdc | 20Vdc | 24Vdc | 26Vdc | At least 2.2A (60W) |
Battery Connection
Battery Supply Connections | Required Contactor Sequencing |
---|---|
Figure 2. Example Battery Supply Connection The image shows an example Battery power supply connection to the drive that provides a supply voltage during rescue operation. |
WarningA suitable protection diode must be fitted to the battery supply as shown in the example to prevent damage to the system. Suitable protection must be provided for all wiring. |
Rescue Operation Battery Supply- Activation
Rescue Mode Running Conditions in Battery Mode | |
---|---|
Figure 3. Running Conditions in Rescue Mode with battery supply All conditions above must be met for the drive to run. Each unfulfilled condition will have a separate issue. | Each of the following conditions must be met for the drive to run in Rescue Operation with a battery supply (P7-01 = 2 : bAtt):
NoteA Speed Reference or Enable Digital Input is not needed in Rescue Mode The drive must not be in a tripped state. |
Figure 4. Activation Conditions for Rescue Mode Conditions to switch from mains to Rescue Mode | To switch into Rescue Mode the drive must be stopped. The drive does not need to be in a healthy state a trip can be present. CautionThe current trip may be disabled in Rescue Mode see: Rescue Operation Battery Supply - Overview for a detailed lost of features disabled in Rescue Mode The IO terminals must have an external voltage supply of at least 20Vdc to activate Rescue Mode. NoteRequired Voltage and Current may differ depending on the external devices connected to the drive Control Terminals. For battery mode P7-01 must be set to 2 : battery or the drive will be stuck in an Under-voltage condition. From default Digital Input 8 is assigned to be Rescue Mode Enable, if a different setting of Macro is used in P1-02 then a different terminal maybe used, or if you are using Macro 0 the Rescue Mode function can be assigned to any Digital Input via Group 12 and selecting option 8 : Rescue Mode. Digital/Relay Outputs can be used to indicate if the drive is operating in rescue mode by setting the Digital/Relay Function to 9 (Rescue Mode Active). |
The direction of travel is governed by the setting of P7-02 (Rescue Operation Function). Click here for more information.
Rescue Mode UPS Supply - Overview
Rescue operation is normally used in the event of a mains borne power failure, with the primary goal of moving the elevator car at a limited motor speed for passenger evacuation, the power source comes from either DC (Batteries) or a UPS power supply.
To setup Rescue Mode with a UPS Supply for the Elevator Core see the next section or use the links below to find a specific section.
Rescue Operation UPS Supply - Introduction
The drive is designed to be operated with a UPS supply while in Rescue Mode.
The available UPS supplies that are compatible with the drive are:
230VAC 1ph
400VAC 2ph
Disabled Functions in Rescue Mode
To allow for operation in Rescue Mode the following functions and trips are disabled/altered:
Function | Rescue Mode |
---|---|
Input Phase Loss Detection | Disabled |
DC bus Ripple detection | Disabled |
Undervolatge trip levels | Reduced - exact values |
Speed Loop Gains | No longer Function Rescue Mode has it's own dedicated gains in (P7-06 and P7-07) |
Motor Autotune | Disabled |
Speed Reference | Disabled - Rescue mode no longer needs a speed reference to run. To run the drive in Rescue Mode the Inputs: STO1/STO2 and a Direction command must be closed. |
Rescue Operation UPS Supply Requirements
Nominal Rating | Minimum Voltage | Maximum Voltage | VA Rating |
---|---|---|---|
230VAC 1ph | 160VAC (226Vdc) | 280VAC | >= 230V x Motor Rated Current |
3 - Rescue Operation UPS Supply - Connection Method
Rescue Operation UPS Supply - Connection Method
UPS Supply Connections | Required Contactor Sequencing |
---|---|
Figure 5. Example UPS Supply Connection The image shows an example UPS power supply connection to the drive that provides a supply voltage during rescue operation. NoteAny Digital Input can be used to activate rescue mode not just Digital Input 8 (DI8). To change the Digital Input for Rescue Mode use P1-02 to select a different Macro or select 0 and create your own Macro. |
WarningCircuit protection must be provided. |
Rescue Operation UPS Supply - Activating Rescue Mode
Conditions to activate Rescue Mode powered from UPS Supply | |
---|---|
Figure 6. Activation Conditions for Rescue Mode | The drive will only run when a direction command is given and the Safety Chain is closed. Direction of travel can be shown on the display by pressing the center button, it is assumed that when a Run up (Forward) command is given the motor rotates clockwise (looking at the motor with the sheave facing you). |
To run in Rescue Mode the following conditions must be fulfilled:
Conditions | Criteria for Conditions to be fulfilled |
---|---|
The Drive must be setup as per the starting instructions for the motor connected to the drive |
|
The Safety Chain must be Closed | STO1 and STO2 must have 24V applied Check P0-03 for STO input status |
A Direction command must be given | Either forward or reverse can be used |
Functional differences in Rescue Mode
During Rescue Mode operation the following functions and trips are disabled/altered:
Function | Rescue Mode |
---|---|
Input Phase Loss Detection | Disabled |
DC bus Ripple detection | Disabled |
Undervoltage trip levels | Reduced - Exact values |
Speed Loop Gains - Group 9 | No Longer Active Rescue Mode has it's own dedicated gains in (P7-06 and P7-07) |
Motor Autotune | Disabled |
Speed Reference | Rescue mode speed is governed by value set in P7-03. To run the drive in Rescue Mode the Inputs: STO1/STO2 and a Direction command must be closed. |
Rescue Mode Functions - Overview
The Elevator Core has multiple different operating functions while in Rescue Mode. Each function can be used to operate the drive differently depending on the system requirements and controller programs.
Below are links to the functions of each operating mode. The functions can be selected using P7-02.
Basic Rescue Mode
Parameter Number | Parameter Name | Default | Available Settings | |||||||
---|---|---|---|---|---|---|---|---|---|---|
P7-01 | Rescue Supply type | 0 : 230V UPS | 0 : 230V UPS 1 : 400V UPS 2 : Battery Operation | |||||||
Select what type of power supply is being used for Rescue Mode Operation
| ||||||||||
P7-02 | Rescue Operation Mode | 0 : Basic Rescue Mode | 0 : Basic Rescue Mode 1 : Light Load Detection 2 : UPS Easiest Direction based on Load Measurement 3 : Energy Optimized | |||||||
There are 3 types of rescue mode operation, the following points of consideration help select the most suitable mode:
| ||||||||||
P7-03 | Rescue Mode Speed | 5.0Hz | P8-02... P8-01 | |||||||
This parameter defines the motor speed during rescue mode operation (when Rescue mode Input is activated), the value is also controlled internally by the power limit function based on the UPS rating entered into parameter P7-04. The actual achievable speed will be limited depending on a number of factors such as DC bus voltage level, motor, travel speed, system efficiencies, estimated value can be calculated as follows : It should also be noted that the level of motor load will affect the available DC bus Voltage; in some cases it may be necessary to reduce the Rescue Speed further in order to prevent nuisance Under Voltage (“U-volt”) trips. NoteP7-03 is the speed that the drive will run at when P7-02 is set to 0. Recommended values are 10% of P4-06 (Motor Rated Speed). | ||||||||||
P7-06 | Rescue Mode Proportional Speed Loop Gain | 10.0% | 0.0 ... 400.0% | |||||||
Sets the Rescue Mode P-Gain to improve speed stability during rescue operation. | ||||||||||
P7-07 | Rescue Mode Integral Speed Loop Gain | 50ms | 0.0 ...1000ms | |||||||
Sets the Rescue Mode I-Gain to improve speed stability during rescue operation. |
Basic Rescue Mode is a operation mode that is available when the drive is in Rescue Mode (P7-15 = 1).
Basic Rescue Mode is the simplest Rescue Mode option in P7-02. When Basic Rescue Mode is selected the drive will simply follow the direction given by the Lift Controller. If the Digital Input corresponding to the run forward command is given the drive will run forward until the UPS/Battery runs out of power, the direction command is removed, a fault occurs or the Safety Chain is opened. The same is applicable for the reverse direction command.
When the drive is running forward the display will show uP and when running in reverse the display will show dn.
The image above shows how to program the drive to use Basic Rescue Mode
While running the drive will indicate direction of travel by the keypad either display uP or dn. When the display shows uP this indicates forward direction and dn indicates a reverse direction. The drive will show the travel speed in Hz next to uP or dn.
All Group 0 monitoring parameters are available to be monitored through the keypad or OptiTools Pro while running in Basic Rescue Mode.
Light Load Detection
Parameter Number | Parameter Name | Default | Available Settings | |||||||
---|---|---|---|---|---|---|---|---|---|---|
P5-01 | Brake Release Time | 0.2s | 0.0...5.0s | |||||||
Sets the delay time, following the contactor Delay time (P3-01) in which it takes for the motor brake to be released (Relay 2) and then drive output frequency ramps up. | ||||||||||
P5-02 | Brake Apply Delay | 0.2s | 0.0...5.0s | |||||||
P7-02 | Rescue Operation Mode | 0 : Basic Rescue Mode | 0 : Basic Rescue Mode 1 : Light Load Detection 2 : UPS Easiest Direction based on Load Measurement 3 : Energy Optimized | |||||||
There are 3 types of rescue mode operation, the following points of consideration help select the most suitable mode:
| ||||||||||
P7-03 | Rescue Mode Speed | 5.00Hz | P8-02...P8-01 | |||||||
This parameter defines the motor speed during rescue mode operation. For Light Load Detection this is the speed reference after the Light Load Detection test has finished and the lightest direction has been found and stored in P7-11. | ||||||||||
P7-06 | Rescue Mode Proportional Speed Loop | 10.0% | 0.0...400.0% | |||||||
Sets the Rescue Mode P-Gain to improve speed stability during rescue operation. | ||||||||||
P7-07 | Rescue Mode Integral Speed Loop Gain | 50ms | 0...1000ms | |||||||
Sets the Rescue Mode I-Gain to improve speed stability during rescue operation. | ||||||||||
P7-08 | Light Load Detection Measurement Time | 1.0s | 0.0...10.0s | |||||||
This parameter determines the time in which the light load detection function runs at the speed set in P7-10 (Light Load Speed Detection Speed) in each direction. | ||||||||||
P7-09 | Light Load Detection Speed | 5.0Hz | P8-02...P8-01 | |||||||
This parameter determines the motor speed during the Light Load Detection test in each direction. | ||||||||||
P7-11 | Light Load Detection Results | 0 : Light direction is forward | 0 : Light direction is forward 1 : Light direction is reverse 2 : Balanced | |||||||
This parameter shows the result of the Rescue Mode function tests when P7-02=1 or P7-02 =2.
|
Light Load Detection is a operation mode that is available when the drive is in Rescue Mode (P7-15 = 1).
To Select Light Load Detections set P7-02 = 1.
Light Load Detection works by calculating the easiest direction to run with a test in each direction.
Operation Steps:
When a run command is given and the Safety Chain is closed, the drive runs in the forward direction for the time specified in P7-08 at the speed set in P7-09.
The drive then stops applies the brakes using P5-01 and P5-02 respectively and then runs in the reverse direction for the same time and speed as the forward direction.
Notice
The drive calculates the easiest direct during the forward and reverse runs and shows the result in P7-11 or in any Digital Output with the setting 17.
The drive then stops again and applies the brake.
The brake is then released and the drive runs in the easiest direction displayed in P7-11 at the speed set in P7-03.
Below is the timing diagram as to how the Light Load Detection functions.
While running the drive will indicate direction of travel by the keypad either display uP or dn. This is valid for the Light Load Detection test and the resultant run.
After the Light Load Detection test has been completed the result can be viewed with either:
P7-11
Digital Output / Relay Output Function set to 17
For both parameters:
0 = Forward (Clockwise)
1 = Reverse (Anti-clockwise)
2 = Balanced (For Digital / Relay Outputs balanced is indicated with a 0).
UPS Easiest Direction based on Measurement
Parameter Number | Parameter Name | Default | Available Settings | |||||||
---|---|---|---|---|---|---|---|---|---|---|
P5-01 | Brake Release Delay | 0.2s | 0.0...5.0s | |||||||
Sets the delay time, following the contactor Delay time (P3-01) in which it takes for the motor brake to be released (Relay 2) and then drive output frequency ramps up. | ||||||||||
P7-03 | Rescue Mode Speed | 5.00Hz | P8-02...P8-01 | |||||||
This Parameter defines the speed the drive will run at when a Run command is given after entering Rescue Mode. | ||||||||||
P7-06 | Rescue Mode Proportional Speed Loop Gain | 10.0% | 0.0...400.0% | |||||||
Sets the Rescue Mode P-Gain to improve speed stability during rescue operation. | ||||||||||
P7-07 | Rescue Mode Integral Speed Loop Gain | 10ms | 0...1000ms | |||||||
Sets the Rescue Mode I-Gain to improve speed stability during rescue operation. | ||||||||||
P7-10 | Load Measurement extended time | 0.0s | 0.0...10.0s | |||||||
Increasing this value can help improve the measurement accuracy of the UPS Easiest Direction based on measurement function. | ||||||||||
P7-11 | Light Load Detection Results | 0 : Light direction is forward | 0 : Light direction is forward 1 : Light direction is reverse 2 : Balanced | |||||||
This parameter shows the result of the Rescue Mode function tests when P7-02=1 or P7-02 =2.
|
UPS Easiest Direction is a operation mode that is available when the drive is in Rescue Mode (P7-15 = 1).
It measures which direction is the easiest direction to run in. Each measurement is taken during the start of each run in mains mode and stores the result in P7-11 so when Rescue Mode is activated the result is already stored with no addition tests before running. While in Rescue Mode once a direction command is given and the run conditions are fulfilled the drive will follow the direction stored in P7-11, similar to Basic Rescue Mode (P7-02 = 0).
To select UPS Easiest Direction set P7-02 = 2.
As shown above UPS Easiest Direction works by:
Set P7-02 = 2 to enable UPS Easiest Direction function.
Set measurement time using P5-01 for the initial measurement then P7-10 if extra time needed. A total of 15 seconds is available (5 in P5-01 and 10 in P7-10).
While in MAINS MODE (P7-15 = 0) run the drive as normal.
Once the drive has stopped P7-11 stores the result.
Notice
When using UPS easiest Direction function P7-11 will store the result of the last travel and only use the last travel measurement as its result, when switching to rescue mode.
When switching to Rescue Mode (P7-15 =0), the drive will run in the direction stored by P7-11 (the direction with the least energy needed to run).
Important
If a balanced scenario (P7-11 = 2) occurs, the drive will automatically switch to a different function of P7-02 depending on the motor control mode selected in P4-01.
The balanced scenarios for each motor type are:
Induction Motor (P4-01 = 1 or 2) - Light Load Detection (P7-02 = 1)
Permanent Magnet Motor (P4-01 = 3) - Basic Rescue Mode (P7-02 = 0)
Energy Optimized
Parameter Number | Parameter Name | Default | Available Settings |
---|---|---|---|
P7-02 | Rescue Operation Mode | 0 : Basic Rescue Mode | 0 : Basic Rescue Mode 1 : Light Load Detection 2 : UPS Easiest Direction based on Load Measurement 3 : Energy Optimized |
There are 3 types of rescue mode operation, the following points of consideration help select the most suitable mode:
| |||
P7-12 | Energy Saving Rescue Unbalancing Max speed | 5.00Hz | P7-13...P8-01 |
The maximum allowable speed in Energy Optimized mode before the brake is applied. | |||
P7-13 | Energy Saving Rescue Minimum Speed | 5.00Hz | P8-02...P8-01 |
This is the minimum speed that must be achieved when UPS saving mode is active, further this speed must be achieved within the time set in P7-14. | |||
P7-14 | Energy Saving Rescue Minimum Speed Time | 0.0s | 0.0...10.0s |
This parameter is used in conjunction with P7-13, when Energy Optimized mode (P7-01 = 2) is active the encoder speed must be at least the value in P7-13 within the time set in P7-14. |
The Energy Optimized function is a operation mode that is available when the drive is in Rescue Mode (P7-15 = 1).
Sometimes referred to as Gravity Mode, Energy Optimized mode switches off the output and controls the Elevator Car by opening and closing the brake at set intervals to control the Elevator Car speed, rather than via a speed control reference.
To select Energy Optimized function set P7-02 = 3.
The above the diagram shows how to activate Energy Optimized function from the parameters.
The operation sequence for Energy Optimized mode is as follows:
Direction command given (Forward / Reverse)
The motor brake releases (Relay 2 Closes)
The drive then either moves or stays still (balanced scenario)
If the drive reaches target speed set in P7-13 in the time set in P7-14 the motor brake applies (Relay 2 Opens)
The brake then opens and closes at a fixed intervals to drop the car down.
This continues until a stop command is given.
Important
If the car does not move (balanced) then the drive automatically switches to a different function in P7-02 depending on the motor control mode selected in P4-01:
Induction Motor (P4-01 = 1 or 2) - Light Load Detection (P7-02 = 1)
Permanent Magnet Motor (P4-01 = 3) - Basic Rescue Mode (P7-02 = 0)
UPS Protection Function
Parameter Number | Parameter Name | Default | Available Settings |
---|---|---|---|
P7-04 | UPS Rating | 0.0kW | 0.0...100.0kW |
P7-05 | Rescue Mode Current Limit | 100.0% | 0.0...200.0% |
P7-16 | UPS overload time limit | 2.0s | 0.0...10.0s |
The drive can be used to protect the external UPS unit. By using P7-04 and P7-16 to set the UPS power rating and overload time respectively the drive can protect the UPS from collapsing/overloading.
The function works by:
Set UPS power rating (in kW) in P7-04 and Overload time limit in P7-16.
Important
If P7-04 is set to 0 then this function is disabled.
When the drive is run in rescue mode if the value in P0-30 exceeds the value set in P7-04 for the total time in P7-16 the drive will trip UPS-L and immediately stop.
Important
The time in P7-16 is total cumulative time during running not consecutive time.
For example if the time in P7-04 is set at 2 seconds. When the drive is run and P0-30 is > P7-04 for 1 second then is below P7-04 for 2 seconds then above P7-04 again for 1 second the drive will trip as the total cumulative time has reached the 2 seconds set in P7-04.
To restart the drive the fault will need to be cleared and a new direction command issued.
Figure 8. UPS Protection Power Function - Timing Diagram The is the standard sequence of operation that applies the the UPS protection function | Figure 9. UPS Protection Power Function - Example Scope Traces This is an example scope traces showing the motor output power cumulatively above the limit set in P7-04 in this case 1.0kW |
The current limit during operation can be set in P7-05. This parameter limits the current operation while running in rescue mode to a percentage of P4-06 (Motor Rated Current), with 100% (default) being the value of P4-06.
Note
P7-05 value is only active in Rescue Mode.
Safe Torque Off (STO)
Important
The overall system designer is responsible for defining the requirements of the overall “Safety Control System” within which the drive will be incorporated; furthermore, the system designer is responsible for ensuring that the complete system is risk assessed and that the “Safety control System” requirements have been entirely met and that the function is fully verified, this must include confirmation testing of the “STO” function before drive commissioning.
The system designer shall determine the possible risks and hazards within the system by carrying out a thorough risk and hazard analysis, the outcome of the analysis should provide an estimate of the possible hazards, furthermore, determine the risk levels and identify any needs for risk reduction. The “STO” function should be evaluated to ensure it can sufficiently meet the risk level required.
Note
The “Safe Torque Off ” function is always enabled in the drive regardless of operating mode or parameter changes made by the user.
The purpose of the “STO “function is to provide a method of preventing the drive from creating torque in the motor in the absence of the “STO“ input signals (STO1 & STO2), this allows the drive to be incorporated into a complete safety control system where “STO“ requirements need to be fulfilled.1
The “STO“ function can typically eliminate the need for electro-mechanical contactors with cross-checking auxiliary contacts as per normally required to provide safety functions.2
The drive has the “STO “Function built-in as standard and complies with the definition of “Safe torque off“as defined by IEC 61800-5-2:2007.
The “STO “Function also corresponds to an uncontrolled stop in accordance with category 0 (Emergency Off), of IEC 60204-1. This means that the motor will coast to a stop when the “STO” function is activated, this method of stopping should be confirmed as being acceptable to the system the motor is driving.
The “STO“ function is recognised as a fail-safe method even in the case where the “STO“ signal is absent and a single fault within the drive has occurred, the drive has been proven in respect of this by meeting the following safety standards :
Standard | Compliance Level |
---|---|
IEC 61800-5-2:2016 | SIL 3 |
EN ISO 13849-1:2015 | PL “e” |
EN 61508 (Part 1 to 7): 2010 | SIL 3 |
EN 60204-1: 2006 & A1: 2009 | Cat 0 |
EN 62061: 2005 & A2: 2015 | SIL CL 3 |
Independent Approval | TBC |
Note : The values achieved above maybe jeopardised if the drive is installed outside of the Environmental limits detailed in Environmental
Caution
Disconnect and ISOLATE the drive before attempting any work on it. The “STO“function does not prevent high voltages from being present at the drive power terminals.
Caution
The “STO“function does not prevent the drive from an unexpected re-start. As soon as the “STO“ inputs receive the relevant signal it is possible (subject to parameter settings) to restart automatically, Based on this, the function should not be used for carrying out short-term non-electrical machinery operations (such as cleaning or maintenance work)
Caution
In some applications additional measures may be required to fulfil the systems safety function needs: the “STO“ function does not provide motor braking. In the case where motor braking is required a time delay safety relay and/or a mechanical brake arrangement or similar method should be adopted, consideration should be made over the required safety function when braking as the drive braking circuit alone cannot be relied upon as a fail-safe method.
Caution
When using Gearless (Permanent Magnet) motors and in the unlikely event of a multiple output power devices failing then the motor could effectively rotate the motor shaft by 180/p degrees (Where p denotes number of motor pole pairs).
When the “STO” inputs are energised, the “STO” function is in a standby state, if the drive is then given a “Start signal/command” (as per the start source method selected in P1-02) then the drive will start and operate normally.
When the “STO” inputs are de-energised then the STO Function is activated and stops the drive (Motor will coast), the drive is now in “Safe Torque Off” mode.
To get the drive out of “Safe Torque Off” mode then any “Fault messages” need to be reset and the drive “STO” input needs to be re-energised.
The STO inputs are positive logic inputs only and are therefore not affected by the setting of parameter P1-43 (Positive/negative logic select).
There are several methods for monitoring the status of the “STO” input, these are detailed below:
In Normal drive operation (Mains AC power, UPS Power or Battery Power), when the drives “STO” input is de-energised (“STO” Function activated) the drive will highlight this by displaying “InHibit”.
Note: If the drive is in a tripped condition then the relevant trip will be displayed and not “InHibit”).
Drive Status parameter
Parameter P0-04 can be viewed to see that STO input status as illustrated below :
Display value | 0 | 0 | |||
---|---|---|---|---|---|
Function | STO Channel 1 | STO Channel 2 |
1 = Input Active
0 = Input InActive
Drive Output Relay and Digital Outputs
Relay 1 or the digital outputs can be used to monitor the status of the STO inputs by setting the function to 8.
For Relay 1 set P1-30 to 8.
For Digital Output 1 (DA1) set P1-15 to 8 and P1-14 to 0
For Digital Output 2 (DA2) set P1-22 to 8 and P1-21 to 0
For Digital Output 3 (DO3) set P1-28 to 8.
Safe Torque Off Fault Codes
Fault Code | Code Number | Description | Corrective Action |
---|---|---|---|
Sto-F | 29 | A fault has been detected within either of the internal channels of the “STO” circuit. | Refer to your Invertek Sales Partner |
Sto-L | 101 | STO1/STO2 signals removed whilst drive running | - |
The total response time is the time from a safety related event occurring to the components (sum of) within the system responding and becoming safe. (Stop Category 0 in accordance with IEC 60204-1)
The response time from the “STO” inputs being de-energised to the output of the drive being in a state that will not produce torque in the motor (“STO” active) is less than 20ms.
The response time from the “STO” inputs being de-energised to the “STO” monitoring status changing state is less than 20ms
The response time from the drive sensing a fault in the STO circuit to the drive displaying the fault on the display/Digital output showing drive not healthy is less than 20ms
Caution
The “STO” wiring shall be protected from inadvertent short circuits or tampering which could lead to failure of the “STO” input signal, further guidance is given in the diagrams below.
In addition to the wiring guidelines for the “STO” circuit below, an “EMC compliant installation” is alos required.
The drive should be wired as illustrated below; the 24Vdc signal source applied to the “STO 1 and STO 2” inputs can be either from the 24Vdc on the drive or from an External 24Vdc power supply (as per the diagram below).
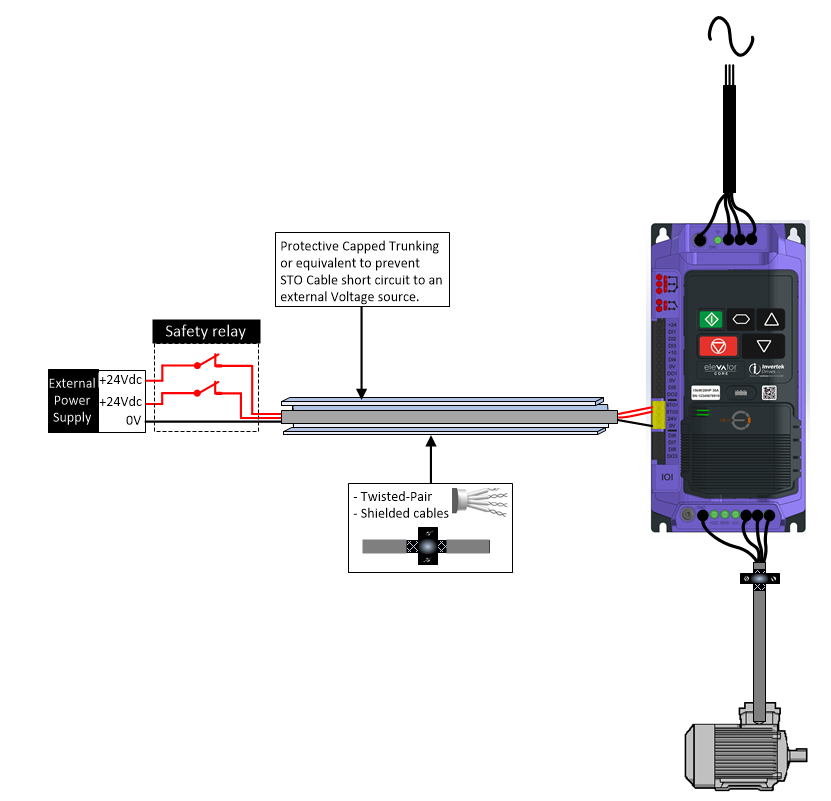
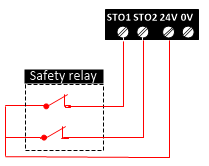
Voltage Rating (Nominal) | STO Logic High | Current Consumption (Maximum) |
---|---|---|
24Vdc | 18Vdc-30Vdc | 100mA |
The safety relay should be chosen so that at minimum it meets the safety standards in which the drive meets.
Standard Requirements | SIL3 or PLe or better (With Forcibly guided Contacts) |
Number of Output Contacts | 2 independent |
Switching Voltage Rating | 30Vdc |
Switching Current | 100mA |
Before commissioning the system the “STO” function should always be tested for correct operation, this should include the following tests:
With the motor at standstill, and a stop command given to the drive (as per the primary command source selected in P1-01):
De-energise the “STO” inputs (Drive will display “InHibit”).
Give a start command (as per the primary command source selected in P1-01) and check that the drive still displays “Inhibit” and that the operation is in line with section 16.1.5 Status and Monitoring
With the motor running normally (from the drive):
De-energise the “STO” inputs
Check that the drive displays “InHibit” and that the motor stops and that the operation is in line with the section Safe Torque Off Status and Monitoring
If drive fault messages are observed refer to section Fault messages and Display messages for further guidance.
Periodic testing of the entire safety circuit within which the drive STO is integrated, is a mandatory requirement. The testing should be repeated every three months or less to ensure the integrity level of the safety circuit is maintained, furthermore the function should be integrity tested following any safety system modifications or maintenance work.
USB-C Port
The drive has a UCB-C connection port as highlighted above, this provides the following facilities: ·
A means to power the drive display up without the need for mains power, this allows the user to navigate and edit the drive parameters using the drives built-in keypad.
A PC connection over USB-C which can be used in conjunction with the Optitools Pro software suite. (Available as a free download from www.invertekdrives.com/variable-frequency-drives/optidrive-elevator-core
Note
When the drive is powered from the USB-C connection only : ·
Other serial communication interfaces will not operate. ·
Parameter editing via keypad or USB-C is allowed..
Caution
Invertek Drives recommends that an isolated cable is used between the drive and the PC.
Elevator Core CANopen Contents
Elevator Core CANopen Communication
The CAN communication profile in the Elevator Core is implemented according to the specification DS301 version 4.02 of CAN in automation (https://www.can-cia.org/). Specific device profiles such as DS402 are not supported.
The CAN communication function is enabled by default after power up. However in order to use any control functions through CAN, the following setting is required: P-12 = 7 or 8.
The CAN communication baud rate can be set by using parameter P-36 (Index 2). Available baud rates are: 125kbps, 250kbps, 500kbps, 1Mbps. (with default setting as 500kbps).
The Node ID is set up through drive address parameter P-36 (Index 1) with the default value of 1.
The tables below show the Index and Sub Index required to address each parameter. All User Adjustable parameters are accessible by CAN, except those that would directly affect the communications.
All parameter values can be read from the drive and written to, depending on the operating mode of the drive – some parameters may not be changed whilst the drive is enabled.
provides the following default COB-ID and functions:
Type | COB-ID | Function |
---|---|---|
NMT | 000h | Network management. |
Sync | 080h | Synchronous message. COB-ID can be configured to other value. |
Emergency | 080h + Node address | Emergency message |
PDO1 (TX) | 180h + Node address | Process data object. PDO1 is pre-mapped and enabled by default. COB-ID can be configured to other value. PDO2 is pre-mapped and disabled by default. Transmission mode, COB-ID and mapping can be configured |
PDO1 (RX) | 200h + Node address | |
PDO2 (TX) | 280h + Node address | |
PDO2 (RX) | 300h + Node address | |
SDO (TX) | 580h + Node address | SDO channel can be used for drive parameter access |
SDO (RX) | 600h + Node address | |
Error Control | 700h + Node address | Guarding and Heartbeat function are supported. COB-ID can be configured to other value. |
NOTE:
The SDO channel only supports expedited transmission.
The can only support up to 2 Process Data Objects (PDO). All PDOs are pre-mapped; however PDO2 is disabled by default. The table below gives the default PDO mapping information.
Customer configuration (mapping) will NOT be saved during power down. This means that the CAN open configuration will restore to its default condition each time the drive is powered up.
Note
Power down is defined as:
Mains Power removed
USB-C Cable removed
24V External supply to IO removed
Elevator Core CANopen Network Management (NMT)
The network management (NMT) service is used to control NMT states of CANopen devices.
An NMT message is a 2-byte CAN frame with COB-ID 0 (000h).
The first byte contains a command specifier which indicates an NMT command.
The second byte contains a Node-ID of a target device
If the node-ID is 0, the message is a global message to all devices on the CANopen network.
Following a Power ON, all CANopen devices will enter the initialisation state. Following completion of the initialisation, the device will switch to pre-operational state and transmit an emergency message to announce the completion of initialisation and availability on the network. In this state, the SDO telegram may be used to configure the node as required, and PDO communication is disabled. The NMT telegram is then used by the Network Controller to switch the device into operational state when configured and ready to operate.
The NMT message has the following format:
COB-ID | NMT Command | Target Node ID |
---|---|---|
0x0000 | 1 Byte | 1 Byte |
Note
The NMT telegram always has COB-ID 0x0000
If the target Node-ID is 0x00, the message is intended for all connected nodes.
The drive supports the following Network Management commands.
NMT Command | Function | Target Node State Transition |
---|---|---|
0x01 | Start Remote Node | Pre-Operational to Operational |
0x02 | Stop Remote Node | Any Sate to Stopped |
0x80 | Enter Pre-Operational | Operational to Pre-Operational |
0x81 | Reset Node | Any State to Initialisation followed by Pre-Operational |
0x82 | Reset Node Communication | Any State to Initialisation followed by Pre-Operational |
Elevator Core Service Data Objects (SDO)
Access to a devices object dictionary is provided by Service Data Object (SDO). SDO permits reading or writing entries in the object dictionary.
The operation of SDOs is on the basis of client/server relationship. The client sends requests and the server responds to those requests.
The SDO communication is peer-to-peer communication.
If an error occurs, for instance an entry does not exist, the device returns a message containing a completion code that represents the error.
SDO message may be used for the following functions:
Read a value
Write a value
By default, SDO messages have the following COB-ID's:
Client to server message has the COB-ID 600h + node ID
Server to client response will have the COB-ID 580h + node ID
SDO messages have the following format:
Byte 0 | Byte 1 | Byte 2 | Byte 3 | Byte 4 | Byte 5 | Byte 6 | Byte 7 |
---|---|---|---|---|---|---|---|
Control Byte | Index (16 Bit) | Sub Index (8 Bit) | Data (Up to 32 Bits) | ||||
See Table Below | LSB | MSB |
The following values for the SDO Control Byte are supported:
Control Byte | Function |
---|---|
0x40 | Read Request (Any Size Data) |
0x4F | Read Request - Single Byte |
0x4B | Read Request - Single Word |
0x43 | Read Request - Double Word |
0x2F | Write Request - Single Byte |
0x2B | Write Request - Single Word |
0x23 | Write Request - Double Word |
60 | Write Response - Successful |
80 | Write Response - Unsuccessful |
The following are examples of using the SDO to read or write data.
Example 1: Client request the value of Index 1018h Sub Index 1 (Vendor ID) from server with node-ID = 1
SDO Message: Client to Server:
COB-ID | Control Byte | Index | Sub Index | Data | |
---|---|---|---|---|---|
0x601 | 0x40 | 0x18 | 0x10 | 0x0 | Not Required |
Note
COB-ID of the request = 0x600 + node ID so for node ID= 1, 0x601
The Index value is transferred with MSB first
The expected response would be:
COB-ID | Control Byte | Index | Sub Index | Data | |
---|---|---|---|---|---|
0x581 | 0x4B | 0x18 | 0x10 | 0x0 | Data Value (Single Word) |
Note
The COB-ID of the response telegram is 0x580 + Node-ID so for Node-ID = 1, the value is 0x581
The Control Byte will indicate the data length, in this example a single word value
Example 2: Client attempts to write the value of Index 1018h Sub Index 1 (Vendor ID) from server with node-ID = 1
In this case, the message from the Client to the server becomes:
COB-ID | Control Byte | Index | Sub Index | Data | |
---|---|---|---|---|---|
0x601 | 0x2B | 0x18 | 0x10 | 0x0 | e.g. 0x0001 |
The Vendor ID value will be read only and therefore the Server should reject the request as follows:
COB-ID | Control Byte | Index | Sub Index | Data | |
---|---|---|---|---|---|
0x581 | 80 | 0x18 | 0x10 | 0x0 | 0x06010002 |
The server will respond with an error code, see below for further information on error codes.
The following table lists some of the common error code response that may be received.
Data Value | Meaning |
---|---|
0x05040000 | SDO Timeout |
0x05040001 | Invalid Control Byte |
0x06010002 | Write Access attempted to a Read Only value |
0x0602000 | SDO Object does not exist |
0x06040041 | The referenced object cannot be mapped to a PDO |
0x06020042 | The size or number of mapped objects results in an invalid PDO size |
0x06070010 | Data type or length is not compatible |
0x06090011 | SDO Sub Index does not exist |
0x06090031 | Parameter value too low |
0x06090032 | Parameter Value too high |
Elevator Core CANopen Specific Object Table
Index | Sub Index | Function | Access | Type | PDO Map | Default Value |
---|---|---|---|---|---|---|
1000h | 0 | Device Type | R | U32 | N | 0 |
1001h | 0 | Error Register | R | U8 | N | 0 |
1002h | 0 | Manufacturer Status Register | R | U16 | N | 0 |
1005h | 0 | COB-ID Sync | RW | U32 | N | 00000080h |
1008h | 0 | Manufacturer Device Name | R | String | N | ODL3 |
1009h | 0 | Manufacturer Hardware Version | R | String | N | x.xx |
100Ah | 0 | Manufacturer Software Version | R | String | N | x.xx |
100Ch | 0 | Guard Time (1ms) | RW | U16 | N | 0 |
100Dh | 0 | Life Time Factor | RW | U8 | N | 0 |
1014h | 0 | COB-ID EMCY | RW | U32 | N | 00000080h+Node ID |
1015h | 0 | Inhibit Time Emergency (100μs) | RW | U16 | N | 0 |
1017h | 0 | Producer Heartbeat Time (1ms) | RW | U16 | N | 0 |
1018h | 0 | Identity Object No. Of entries | R | U8 | N | 4 |
1 | Vendor ID | R | U32 | N | 0x0000031A | |
2 | Product Code | R | U32 | N | Drive Dependent | |
3 | Revision Number | R | U32 | N | x.xx | |
4 | Serial Number | R | U32 | N | Drive Dependent | |
1200h | 0 | SDO Parameter No. Of entries | R | U8 | N | 2 |
1 | COB-ID Client -> Server (RX) | R | U32 | N | 00000600h+Node ID | |
2 | COB-ID Server -> Client (TX) | R | U32 | N | 00000580h+Node ID | |
1400h | 0 | RX PDO1 comms param. no. of entries | R | U8 | N | 2 |
1 | RX PDO1 COB-ID | RW | U32 | N | 40000200h+Node ID | |
2 | RX PDO transmission type | RW | U32 | N | 254 | |
1401h | 0 | RX PDO2 comms param. no. of entries | R | U8 | N | 2 |
1 | RX PDO2 COB-ID | RW | U32 | N | C0000300h+Node ID | |
2 | RX PDO2 transmission type | RW | U8 | N | 0 | |
1600h | 0 | RX PDO1 1 mapping / no. of entries | RW | U8 | N | 4 |
1 | RX PDO1 1st mapped object | RW | U32 | N | 20000010h | |
2 | RX PDO1 2nd mapped object | RW | U32 | N | 20010010h | |
3 | RX PDO1 3rd mapped object | RW | U32 | N | 20030010h | |
4 | RX PDO1 4th mapped object | RW | U32 | N | 00060010h | |
1601h | 0 | RX PDO2 1 mapping / no. of entries | RW | U8 | N | 4 |
1 | RX PDO2 1st mapped object | RW | U32 | N | 00060010h | |
2 | RX PDO2 2nd mapped object | RW | U32 | N | 00060010h | |
3 | RX PDO2 3rd mapped object | RW | U32 | N | 00060010h | |
4 | RX PDO2 4th mapped object | RW | U32 | N | 00060010h | |
1800h | 0 | TX PDO1 comms parameter number of entries | R | U8 | N | 3 |
1 | TX PDO1 COB-ID | RW | U32 | N | 40000180h+Node ID | |
2 | TX PDO1 transmission type | RW | U8 | N | 254 | |
3 | TX PDO1 Inhibit time (100μs) | RW | U16 | N | 0 | |
1801h | 0 | TX PDO2 comms param no. of entries | R | U8 | N | 3 |
1 | TX PDO2 COB-ID | RW | U32 | N | C0000280h+Node ID | |
2 | TX PDO2 transmission type | RW | U8 | N | 0 | |
3 | TX PDO2 Inhibit time (100μs) | RW | U16 | N | 0 | |
1A00h | 0 | TX PDO1 mapping / no. of entries | RW | U8 | N | 4 |
1 | TX PDO1 1st mapped object | RW | U32 | N | 200A0010h | |
2 | TX PDO1 2nd mapped object | RW | U32 | N | 200B0010h | |
3 | TX PDO1 3rd mapped object | RW | U32 | N | 200D0010h | |
4 | TX PDO1 4th mapped object | RW | U32 | N | 200E0010h | |
1A01h | 0 | TX PDO2 mapping / no. of entries | RW | U8 | N | 4 |
1 | TX PDO2 1st mapped object | RW | U32 | N | 200F0010h | |
2 | TX PDO2 2nd mapped object | RW | U32 | N | 20100010h | |
3 | TX PDO2 3rd mapped object | RW | U32 | N | 20110010h | |
4 | TX PDO2 4th mapped object | RW | U32 | N | 200C0010h |
Elevator Core PDO Transmission Type
Various transmission modes can be selected for each PDO. For RX PDO, the following modes are supported:
Transmission Type | Mode | Description |
---|---|---|
0-240 | Synchronous | The received data will be transferred to the drive active control register when the next sync message is received. |
254, 255 | Asynchronous | The received data will be transferred to the drive active control register immediately without delay. |
For TX PDO, the following modes are supported:
Transmission Type | Mode | Description |
---|---|---|
0 | Acyclic synchronous | TX PDO will only be sent out if the PDO data has changed and PDO will be transmitted on reception of SYNC object. |
1-240 | Cyclic synchronous | TX PDO will be transmitted synchronously and cyclically. The transmission type indicates the number of SYNC object that are. |
254 | Asynchronous | TX PDO will only be transferred once corresponding RX PDO has been received. |
255 | Asynchronous | TX PDO will only be transferred anytime if PDO data value has changed. |
Elevator Core CANopen PDO Default Mapping
Objects No. | Mapped Object | Length | Mapped Function | Transmission Type | |
---|---|---|---|---|---|
RX PDO1 | 1 | 2000h | Unsigned 16 | Control Word | 254 Valid immediately |
2 | 2001h | Integer 16 | Speed reference | ||
3 | 2003h | Unsigned 16 | Reserved | ||
4 | 0006h | Unsigned 16 | Reserved | ||
TX PDO1 | 1 | 200Ah | Unsigned 16 | Drive status register | 254 Send after receiving RX PDO1 |
2 | 200Bh | Integer 16 | Motor speed Hz | ||
3 | 200Dh | Unsigned 16 | Motor current | ||
4 | 2010h | Integer 16 | Drive temperature | ||
RX PDO2 | 1 | 0006h | Unsigned 16 | Dummy | 254 |
2 | 0006h | Unsigned 16 | Dummy | ||
3 | 0006h | Unsigned 16 | Dummy | ||
4 | 0006h | Unsigned 16 | Dummy | ||
TX PDO2 | 1 | 2011h | Unsigned 16 | DC bus voltage | 254 |
2 | 2012h | Unsigned 16 | Digital input status | ||
3 | 2013h | Integer 16 | Analog input 1 (%) | ||
4 | 2014h | Integer 16 | Analog input 2 (%) |
Elevator Core CANopen Physical Connectivity
Fieldbus Network | Required Option | Supported Communication Types |
---|---|---|
CiA301 | None - Built in as Standard | 2x PDO & SDO |
The drive has a built-in RJ45 port for connection of a CANopen network, this is highlighted by the arrow in the image below.
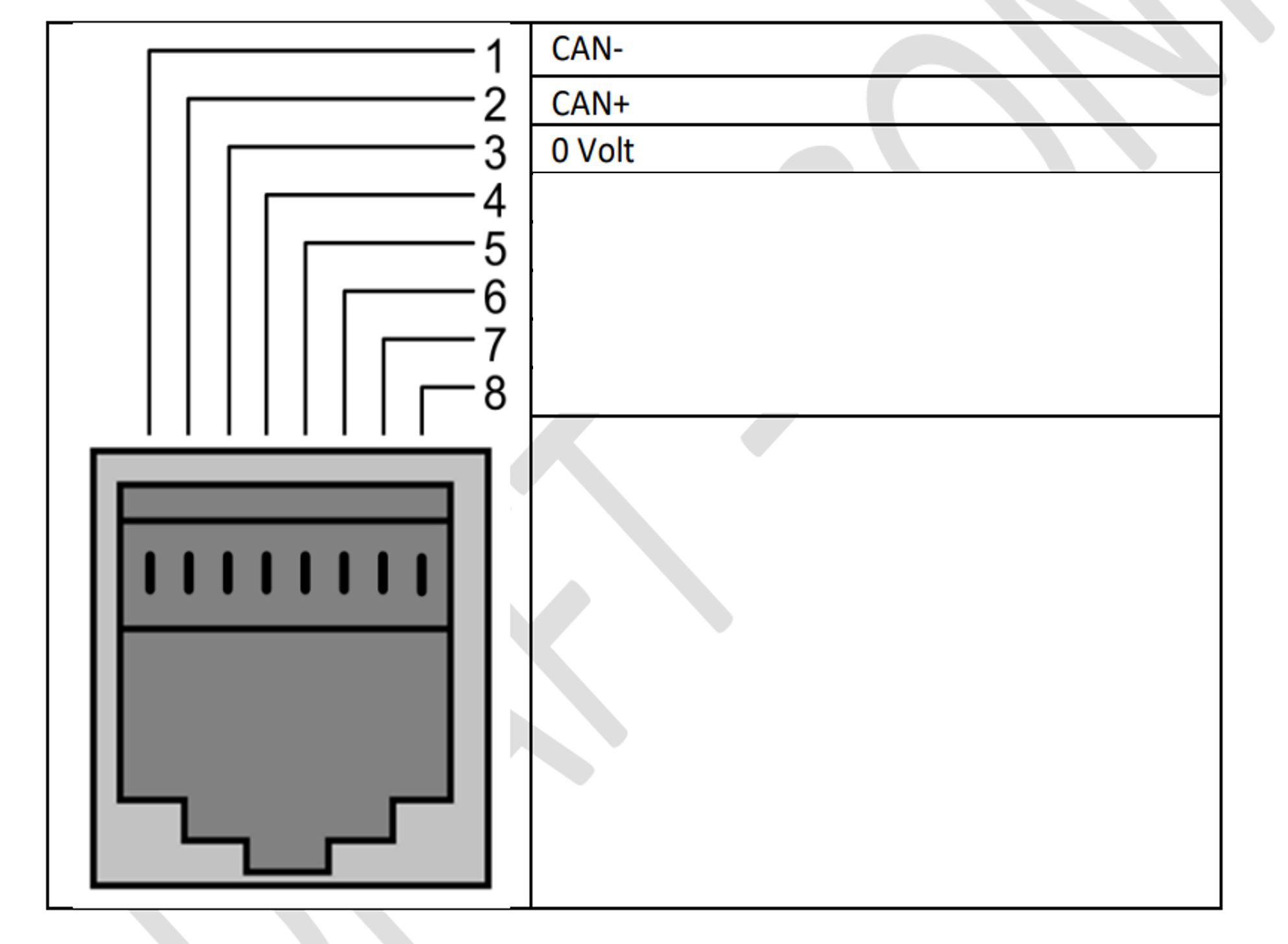
Caution
Always Ensure 0V connection is present.
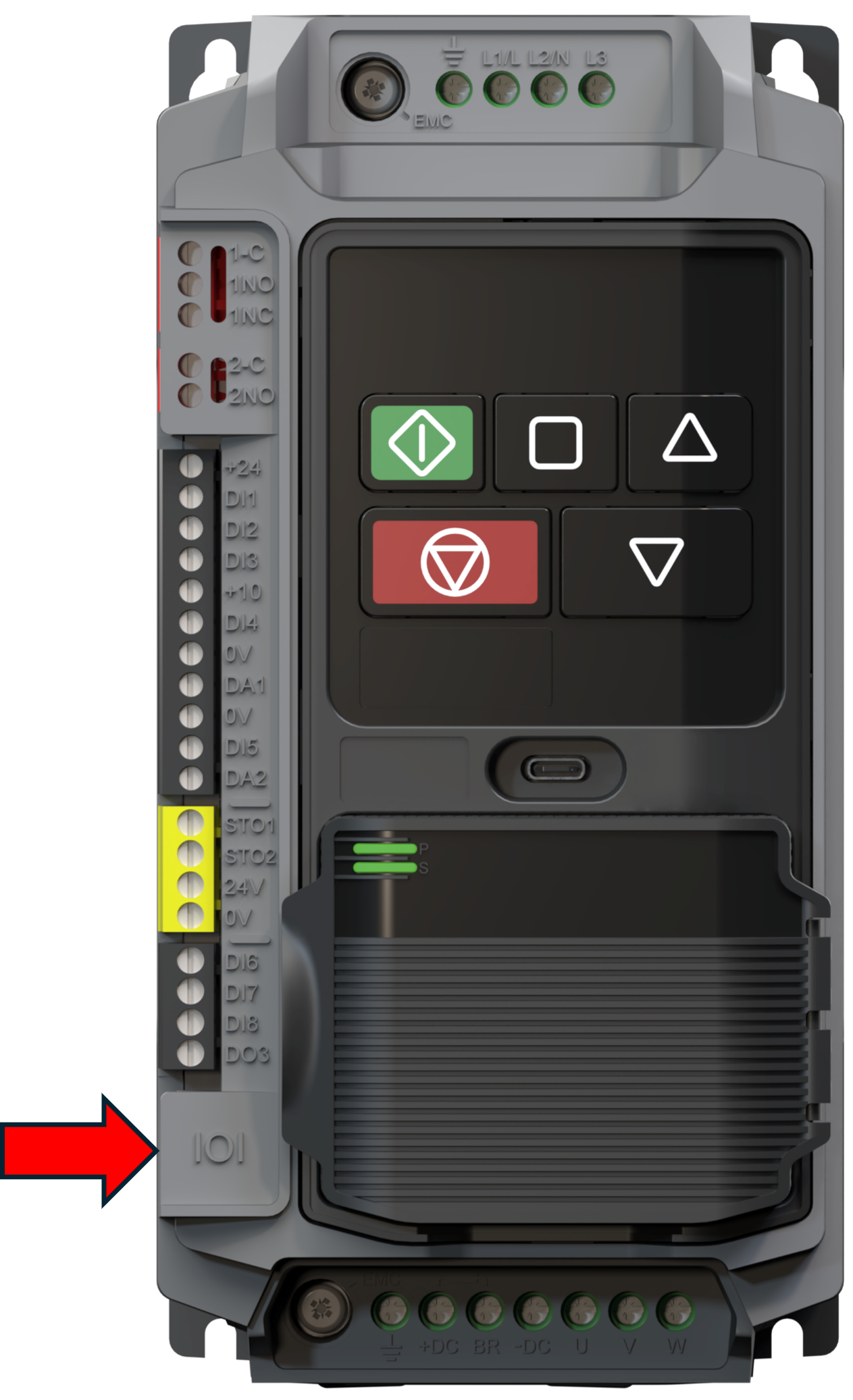
Notice
A Network terminating resistor (120Ω) may be used at the end of the network to reduce noise.
Elevator Core CANopen Communication Setup Parameters
The following Parameters must be set for the drive to be controlled over CANopen
Configure the Command Source to CANopen in P1-01.
Parameter Number
Parameter Name
Default
Available Settings
P1-01
Primary Command Source
0 : Terminal
0 : Terminal
1 : FieldBus
2 : CANopen
Set the CANopen Address in P2-07.
Parameter Number
Parameter Name
Default
Available Settings
P2-07
CANopen Address
1
1...127
Set the CANopen Baud Rate in P2-08.
Parameter Number
Parameter Name
Default
Available Settings
P2-08
CANopen Baud Rate
1 : 500 kbps
0 : 125 kbps
1 : 250 kbps
2 : 500 kbps
3 : 1Mbps
Set Heartbeat communication loss reaction in P2-09
Parameter Number
Parameter Name
Default
Available Settings
P2-09
CANopen comms loss reaction
2 : Ramp to Stop Only (No Trip)
0 : Trip
1 : Ramp to stop then Trip
2 : Ramp to Stop Only (No Trip)
3 : Run at Inspection Speed (P8-09)
Elevator Core CANopen Group 1 - Group 12 Parameter Access
All parameters can be accessed over CAN communication regardless of setting in P1-01.
Each parameter has it's own specific Object ID that can be calculated by the formula: Object ID = 2000h + (Group * 100) + Parameter Number
For example using the above formula to calculate P8-01 (Maximum Frequency):
Hexadecimal Version: 2000h + (8h * 64h) + 1h = 2321h
Decimal Version: 8192 + (8 * 100) + 1 = 8993
So if you were using Hexadecimal to write the Object ID you would enter 2321h or 8993 is using decimal.
Elevator Core CANopen Drive Control Word Format
Bit Number | 15 | 14 | 13 | 12 | 11 | 10 | 9 | 8 | 7 | 6 | 5 | 4 | 3 | 2 | 1 | 0 |
---|---|---|---|---|---|---|---|---|---|---|---|---|---|---|---|---|
Byte | High Byte | Low Byte |
Bit 0: Run Forward / Stop command: Set to 1 to enable the drive and run forward. Set to 0 to stop the drive.
Bit 1: Run Reverse / Stop command: Set to 1 to enable the drive and run reverse. Set to 0 to stop the drive.
Bit 2: Reset request. Set to 1 in order to reset the drive if drive is under trip condition.
User must clear this bit when drive is under normal condition to prevent un-expected reset.
Important
Drive must be set to CANopen command source in P1-01 to run the drive via CANopen.
To run the drive using the Control Word the following conditions must be fulfilled:
The Safety Chain is closed (STO1 and STO2 are closed)
P1-01 must be set to 2 : CANopen
The drive must not be in a tripped state
All commissioning steps are completed
Elevator Core Drive Status Objects
When controlling the drive through any fieldbus network the registers below can be used to provide a simple status feedback from the drive. Registers 6, 7 and 8 are pre-mapped to the first CAN PDO.
CANopen Index | Sub Index | PDO Map | Parameter Number | Upper Byte | Lower Byte | Format | Type | Scaling |
---|---|---|---|---|---|---|---|---|
200Ah | 0 | Y | - | Status Word | WORD | RO | N/A | |
200Bh | 0 | Y | - | Output Frequency | S16 | RO | 1dp, e.g., 100 = 10.0Hz | |
200Dh | 0 | Y | P0-25 | Motor Current | U16 | RO | 1dp, e.g., 100 = 10.0A | |
200Eh | 0 | Y | P0-28 | Motor Torque | S16 | RO | 4096 = 100% | |
200Fh | 0 | Y | P0-29 | Motor Power | U16 | RO | 0dp e.g., 1 = 1°C | |
2010h | 0 | Y | P0-48 | Drive Temperature | U16 | RO | N/A | |
2011h | 0 | Y | P0-40 | DC Bus Voltage | U16 | RO | N/A | |
2012h | 0 | Y | P0-01 / P0-02 | Digital Input States | U16 | RO | N/A | |
2012h | 1 | Y | P0-03 | STO Input State | U8 | RO | N/A | |
2013h | 0 | Y | P0-57 | Analog Input 1 Percentage | S16 | RO | 1dp, e.g 10 = 1% | |
2013h | 1 | Y | P0-59 | Analog Input 2 Percentage | S16 | RO | 1dp, e.g 10 = 1% | |
2014h | 0 | Y | P0-07 | Analog Output 1 Value | S16 | RO | N/A | |
2014h | 1 | Y | P0-08 | Analog Output 2 Value | S16 | RO | N/A | |
2015h | 0 | Y | P0-04 | Relay 1 State | U8 | RO | N/A | |
2015h | 1 | Y | P0-05 | Relay 2 State | U8 | RO | N/A |
Bit | Status 0 | Status 1 |
---|---|---|
0 | Drive not Ready | Drive Ready |
1 | Drive Stopped | Drive Running |
2 | Drive Healthy | Drive Tripped |
3 | Reserved | Reserved |
4 | Reserved | Reserved |
5 | Reserved | Reserved |
6 | Drive below Target Speed | Drive at Target Speed |
7 | Drive running >= P8-02 | Drive running <= P8-02 |
8 | Motor Current < P4-03 | Motor current > P4-03 Overload Condition) |
9 | No Mains Loss / Reverse Power not detected | Mains Loss / Reverse Power detected |
10 | Heatsink temperature below 85°C | Heatsink temperature over 85°C |
11 | PCB temperature below 80°C | PCB temperature over 80°C |
12 | Frequency Foldback not Active | PWM switching frequency foldback is active |
13 | Running Forward (CW) | Running in reverse (CCW) |
14 | Reserved | Reserved |
15 | Reserved | Reserved |
Elevator Core CANopen EDS File
The has an associated EDS file that can be downloaded from: Elevator Core CANopen EDS
Fault messages and Display messages
Display message | No. | Description | Corrective Action/Further information |
---|---|---|---|
Ai-Los | 59 | Analog input signal loss | |
AtF-01 | 40 | Autotune Failed | Measured motor stator resistance varies between phases. Ensure the motor is correctly connected and free from faults. Check the windings for correct resistance and balance. |
AtF-02 | 41 | Measured motor stator resistance is too large. Ensure the motor is correctly connected (motor contactor is closed) and free from faults. Check that the power rating corresponds to the power rating of the connected drive. | |
AtF-03 | 42 | Measured motor inductance is too low. Ensure the motor is correctly connected and free from faults. | |
AtF-04 | 43 | Measured motor inductance is too large. Ensure motor is correctly connected and free from faults. Check that the power rating corresponds to the power rating of the connected drive. | |
AtF-05 | 44 | Measured motor parameters are not convergent. Ensure the motor is correctly connected and free from faults. Check that the power rating corresponds to the power rating of the connected drive. | |
AtF-06 | 45 | Encoder offset measurement failed | Drive has failed to measure the Encoder offset value using autotune method 2 in P4-08. Normally Occurs on Permanent Magnet motors with Surface Mounted magnets. |
Atf-nA | 109 | Selected Autotune method incorrect for the selected Motor | Use Autotune 1 (P4-08=1). |
bF-Err | 46 | Brake Release Monitoring- Warning | Check Brake micro-switches, and brake release monitoring time set in P5-05 is suitable. |
bF-Loc | 47 | Brake Release Monitoring- Lockout | |
BuS-08 | 67 | Internal Communication Error | Power Cycle Drive, remove all power sources including USB-C. If error still shows after power cycle, then Contact your local Invertek representative. |
BuS-.. | Internal Communication Error | Contact your local Invertek representative. | |
CC | - | Motor Contactor Closing/opening delay time | Shown during the period set in parameter(P3-01) motor contactor Closing/Opening time allowance |
CF-Err | 96 | Motor Contactor feedback Error | Motor contactor is in wrong state as indicated by feedback signal from contactor. |
CF9-Ch | 77 | Drive configuration data changed. | |
CF9-dF | 78 | Drive configuration mismatch PS/IO | |
CF9-Er | 79 | Drive configuration data missing or corrupt. | |
CrFLT | 30.3 | Critical Module Error | |
dAtA-3 | 98 | Internal data error | |
data-E | 19 | Internal memory fault. |
Parameters not saved, defaults reloaded. Try again. If problem recurs, refer to your Invertek Sales Partner |
data-F | 17 | Internal memory fault. | Parameters not saved, defaults reloaded. Try again. If problem recurs, refer to your Invertek Sales Partner. |
Ed-dAt | 30.7 | Encoder Feedback Error | Data Loss - Fault with CLK or DATA lines |
Ed-Pd | 30.71 | Propagation Delay Error (Cable too long) | |
Ed-LoS | 30.72 | Comms Error (excessive signal drop out) or Line Loss whilst drive is running. | |
Ed-inc | 30.73 | Encoder Incompatible | |
Ed-AOS | 30.74 | Endat ABS Overspeed | |
Ed-SOS | 30.75 | Endat SC Overspeed | |
Ed-SAb | 30.76 | Sin Cos Line Loss | |
Ed-1 | 30.77 | Endat Error - Light Unit Failure | |
Ed-2 | 30.78 | Endat Error - Signal Amplitude to low | |
Ed-3 | 30.79 | Endat Error - Position calculation error | |
Ed-4 | 30.8 | Endat Error - Supply Overvoltage | |
Ed-5 | 30.81 | Endat Error - Supply Undervoltage | |
Ed-6 | 30.82 | Endat Error - Supply Overcurrent | |
Ed-7 | 30.83 | Endat Error - Battery need replacing | |
Ed-8 | 30.84 | Encoder Reported Unknown Error | |
Enc-CL | Tbc | Encoder Module not fitted | Encoder I/O Comms Loss - Confirm module is fitted and pushed fully home. |
Enc-PP | 99 | Encoder Pulse per revolution parameter (P6-03) set as 0 with Encoder Enabled (P6-04>0) | |
E-trip | 11 | External trip | E-trip requested on control input terminals. Some settings of P1-02 require a normally closed contact to provide an external means of tripping the drive if an external device develops a fault. If a motor thermistor is connected check if the motor is too hot. |
Enc-Er | 30 | Encoder Feedback Faults (Only visible when an encoder module is fitted and enabled) | Will also show sub-trip code to Encoder communication /data loss |
EncCF8 | Encoder Configuration Error | Encoder type has not been set in parameter P6-04. | |
EncCF9 | 100 | Encoder Configuration Error | Encoder offset measurement has been attempted with Encoder disabled, check Encoder is Enabled (P6-05=1) |
E-103 | 103 | Unexpected PS Firmware Change | |
E-250 | 250 | Internal Error | |
E-251 | 251 | Module not supported | |
E-252 | 252 | IO not supported | |
E-253 | 253 | Hardware ID not supported | |
E-254 | 254 | Drive ID not supported | |
E-255 | 255 | ||
Flt-dc | 13 | Excessive DC Ripple | The DC Bus Ripple Voltage level is displayed in parameter P0-41. Check all three supply phases are present and within the 3% supply voltage level imbalance tolerance. Reduce the motor load. |
F-Ptc | 21 | Motor PTC Over Temperature | The connected motor PTC device has caused the drive to trip |
F-tY | Motor KTY84 Thermistor Fault | ||
FaN-F | 22 | Cooling Fan Fault | Check and if necessary, replace the drive internal cooling fan |
HtLO | 30.29 | Quadrature TTL Over-speed | |
h O-I | 15 | Instantaneous over current on drive output. | Refer to fault 3 below |
I.t-trp | 04 | Drive has tripped on overload after delivering >100% of value in P4-03 for a period of time. | Increase acceleration rate (P8-03) or reduce the load. Check motor cable length does not exceed exceeds 100m (screened cable), or 150m (un-screened cable). Ensure the motor nameplate parameters are correctly entered in P4-02, P4-03, P4-04, P4-05. If operating in Vector mode (P4-01 – 0 or 1), also check the motor power factor in P4-07 and ensure an autotune has been successfully completed for the connected motor. Check the load mechanically to ensure it is free, and that no jams, blockages or other mechanical faults exist. If operating a Gearless motor check the encoder offset is correct and try repeating the measurement to confirm consistent values are being measured (P4-08=3) |
InLoSS | 102 | 3 Phase input loss whilst running | |
IC-A | 30.2 | Encoder Channel A Fault | |
IC-B | 30.23 | Encoder Channel B Fault | |
IC-2 | 30.26 | Encoder Channel Z Fault | |
L1-LoS | 92 | L1 Phase is not present | |
L2-LoS | 93 | L2 Phase is not present | |
L3-LoS | 94 | L3 Phase is not present | |
no-Flt | 0 | No Fault | |
Odr-Er | 55 | Wrong Run Sequence | Confirm STO and direction input is applied before speed commands. This function can be disabled by setting P11-23 to 1:Disabled |
O-heat | 23 | Ambient Temperature too High | The measured temperature around the drive is above the operating limit of the drive. Ensure the drive internal cooling fan is operating. Ensure that the required space around the drive as shown in section 7.2, and that the cooling airflow path to and from the drive is not restricted. Increase the cooling airflow to the drive. Reduce the effective switching frequency setting in parameter P11-05. Reduce the load on the motor / drive. |
Out-F | 26 | Drive output fault | Drive output fault, Confirm all 3 motor phases are connected, check that output contactors are closing fully, not arcing, or not opening whilst the drive is running. Confirm contactor control connections to the drive are correct. |
O-t | 08 | Heatsink over temperature | The heatsink temperature can be displayed in P0-48. Check the drive ambient temperature Ensure the drive internal cooling fan is operating Ensure there is the required space around the drive as shown in section 7.2, and that the cooling airflow path to and from the drive is not restricted Reduce the effective switching frequency setting in parameter P11-05. Reduce the load on the motor / drive |
OI-b | 01 | Brake channel over current | Ensure the connected brake resistor is above the minimum permissible level for the drive – refer to the ratings shown in section 6. Check the brake resistor and wiring for possible short circuits. |
OL-br | 02 | Brake resistor overload | The drive software has determined that the brake resistor is overloaded (based on the values entered in P3-04 and P3-05), and trips to protect the resistor. Always ensure the brake resistor is being operated within its designed parameter before making any parameter or system changes. To reduce the load on the resistor, increase deceleration time P8-04, reduce the load inertia or add further brake resistors in parallel, observing the minimum resistance value for the given drive. |
O-I | 03 | Instantaneous over current on drive output (Triggered from Drive Output Current Measurement) | Fault Occurs on Drive Enable Check the motor and motor connection cable for phase – phase and phase – earth short circuits. Check the load mechanically for a jam, blockage, or stalled condition. Is the drive sized correctly for the connected motor? Ensure the motor nameplate parameters are correctly entered in P4-02, P4-03, P4-04, P4-05. If operating in Vector mode (P4-01 – 0 or 1), also check the motor power factor in P4-07 and ensure an autotune has been successfully completed for the connected motor. If operating in Enhanced V/F mode reduce the Boost voltage setting in P4-09. Increase the acceleration ramp up time in P8-03. If the connected motor has a holding brake, ensure the brake is correctly connected and controlled, and is releasing correctly. If operating a Gearless motor check the encoder offset is correct and try repeating the measurement to confirm consistent values are being measured (P4-08=3). Fault Occurs When Running If operating in Vector mode (P4-01 – 0 or 1, 3), reduce the speed loop gains as described in section 13.3. |
Out-PH | 49 | Output phase loss | Check all 3 motor phases are connected, confirm that motor contactor is closing. |
OUt-U | 88 | U Phase PWM output Loss | |
OUt-v | 89 | V Phase PWM output Loss | |
OUtww | 90 | W Phase PWM output Loss | |
O-Volt | 06 | Over voltage on DC bus | Check that the lift has been correctly balanced. Check that a brake resistor is connected correctly to terminals +DC and BR. Check the resistance of the brake resistor complies with the values in section 6. If the fault occurs on stopping or during deceleration, increase the deceleration time in P8-04. If operating in Vector Mode (P4-01 = 0,1,3), reduce the speed loop gains in section 13.3. Check that the mains voltage level is within the range detailed in section 6. The value of the DC Bus Voltage can be displayed in P0-40. |
Ot-br | 58 | Brake resistor overtemperature | Based on Brake resistor over temperature feedback via drive terminals. |
OI-U | 81 | Output (Motor) U Phase overcurrent | |
OI-v | 82 | Output (Motor) V Phase Loss overcurrent | |
OI-ww | 83 | Output (Motor) W Phase Loss overcurrent | |
OI-2 | 84 | Ground current fault | |
Oph-U | 85 | Output (Motor) U Phase Loss | U phase is not connected to the drive, check that output contactors are closing fully, not arcing, or not opening whilst the drive is running, and see P10-08 (Motor connected check). |
Oph-V | 86 | Output (Motor) V Phase Loss | V phase is not connected to the drive, check that output contactors are closing fully, not arcing, or not opening whilst the drive is running, and see P10-08 (Motor connected check). |
Oph-wW | 87 | Output (Motor) W Phase Loss | W phase is not connected to the drive, check that output contactors are closing fully, not arcing, or not opening whilst the drive is running, and see P10-8 (Motor connected check). |
O-SPd | 91 | Shown when the rotor speed is higher than 150% of maximum speed (P8-01) (immediate trip) or higher than 125% maximum speed (P8-01) for more than 100ms, whichever happens first. | |
P-ASY | 95 | Input phase voltage imbalance | |
P-def | 10 | Factory Default parameters have been loaded | Press STOP key, the drive is now ready to be configured for the required application |
P-LOss | 14 | Input phase loss trip | Drive intended for use with a 3 phase supply, one input phase has been disconnected or lost. |
Prog-2 |
| ||
PE | 30.2 | Parameterisation Error | |
PS-trp | 05 | Instantaneous over current on drive output (Triggered from Power Module Current Measurement) | Refer to fault 3 above |
SC-Ab | 30.5 | Sin Cos A B Line Loss | |
SC-C | 30.51 | Sin Cos C Line Loss | |
SC-d | 30.52 | Sin Cos D Line Loss | |
Sc-F01 | 50 | Modbus comms fault | A valid Modbus telegram has not been received within the watchdog time limit set in P5-06. Check the network master / PLC is still operating, Check the connection cables. Increase the value of P2-06 to a suitable level. |
Sc-F02 | 51 | CAN Open comms trip | A valid CAN open telegram has not been received within the watchdog time limit set in P5-06. Check the network master / PLC is still operating, Check the connection cables. Increase the value of P2-06 to a suitable level. |
Sc-F03 | 52 | Communications Option Module Fault | Internal communication to the inserted Communication Option Module has been lost. Check the module is correctly inserted. |
Sc-F04 | 53 | IO card comms trip | Internal communication to the inserted Option Module has been lost. Check the module is correctly inserted. |
SC-OS | 30.53 | Sin Cos Over-speed | |
SC-LoS | 97 |
| |
SC-th | 27 | Motor thermistor short circuit | Check motor thermistor for wiring faults, check thermistor has not failed. |
Shos | 30.1 | Motor Over Speed | |
Sp-Err | 31 | Speed Error | Encoder Speed Error. The % error between the estimated (open loop)/measured encoder feedback speed and the actual motor speed is greater than the value set in P6-11 for the time set in P6-12.
|
Sto-L | 101 | STO inputs opened whilst drive running | |
Sto-F | 29 | Internal STO circuit Error | Check supply to terminals STO1 and STO2 is >18V, otherwise Refer to your Invertek Sales Partner |
ttlO | 30.3 | Quadrature HTL Over-speed | |
th-FLt | 16 | Faulty thermistor on heatsink. | Refer to your Invertek Sales Partner. |
Tr-Lt | Tbc | Travel limit counter reached | The value set in parameter P10-05 (Travel Direction Change Counter limit) has been reached. |
U-Def | 20 | User Parameter Defaults | User Parameter defaults have been loaded. Press the Stop key. |
U-Volt | 07 | Under voltage on DC bus | This occurs routinely when power is switched off. If it occurs during running, check the incoming supply voltage, and all connections into the drive, fuses, contactors etc. If in rescue mode confirm that the voltage is within the range detailed in section 16 If in rescue mode try decreasing rescue mode speed (P7-03) |
UPS-L | 110 | UPS Overload | Whilst operating in Rescue mode the output power to the motor exceeded the value of UPS rating (P7-04) for the time set in parameter (P7-16) UPS Overload Time Limit, Reduce Rescue Mode Speed/Motor Load. |
U-t | 09 | Under temperature | Trip occurs when ambient temperature is less than -20°C. The temperature must be raised over -20°C in order to start the drive. |
USB C | - | Drive is being powered from the USB_C port on the front of the drive. | |
USB P | - | Drive is being powered from the USB_C port on the front of the drive and data transmitting via USB_C is disabled (P2-13 set to 0) | |
Usr-PS | - | Save User defaults action has been performed | Shown when P11-01 is set to 1 to save values as user default parameters. |
USr-cL | - | Clear User defaults action has been performed | Shown when P11-01 is set to 2 to clear user default parameters. |
4-20 F | 18 | 4-20mA Signal Lost | The reference signal on Analog Input 1 or 2 (DI4/DI5) has dropped below the minimum threshold of 3mA. Check the signal source and wiring to the drive terminals. |
4-20 I | 28 | Current input >25mA | Reduce current to maximum of 20mA on terminals DI4/DI5 |
Additional Information for UL Compliance
The drive is designed to meet the UL requirements. In order to ensure full compliance, the following must be fully observed.
For an up to date list of UL compliant products, please refer to UL listing NMMS.E226333.
In order to ensure full compliance, the requirements set out in the below table must be fully observed
Input Power Supply Requirements | ||||
---|---|---|---|---|
Supply Voltage | 200-240V for 230 Volt Single Phase input rated units + / - 10V variation allowed, Maximum 240V RMS . | |||
200-240V for 230 Volt 3-Phase input rated units + / - 10V variation allowed, Maximum 240V RMS . | ||||
380 – 480 Volts for 400 Volt input rated units, + / - 10% variation allowed, Maximum 500V RMS | ||||
Imbalance | Maximum 3% voltage variation between phase – phase voltages allowed | |||
All drives have phase imbalance monitoring. A phase imbalance of > 3% will result in the drive tripping. For input supplies which have supply imbalance greater than 3% (typically the Indian sub-continent & parts of Asia Pacific including China) Invertek Drives recommends the installation of input line reactors. | ||||
Frequency | 50 – 60Hz + / - 5% Variation | |||
Short Circuit Capacity | Voltage Rating | Min kW (HP) | Max kW (HP) | Maximum supply short-circuit current |
230V Single Phase input rated units | 2.2 (3) | 2.2 (3) | 100kA rms (AC) | |
230V 3- Phase input rated units | 4 (5) | 18.5 (25) | ||
400 Volt input rated units | 4 (5) | 22 (30) | ||
All the drives in the above table are suitable for use on a circuit capable of delivering not more than the above specified maximum supply short-circuit Amperes symmetrical with the specified maximum supply voltage. | ||||
Mechanical Installation Requirements | ||||
The drive is intended for indoor installation within controlled environments which meet the condition limits shown in the section Environmental | ||||
Electrical Installation Requirements | ||||
Incoming power supply connection must be according to section xxxx | ||||
Suitable Power and motor cables should be selected according to the data shown in section xxxx and the National Electrical Code or other applicable local codes. | ||||
Motor Cable | 75°C copper stranded or similar. | |||
Power cable connections and tightening torques are shown in section xxxx | ||||
Integral Solid Sate short circuit protection does not provide branch circuit protection. Branch circuit protection must be provided in accordance with the national electrical code and any additional local codes. Ratings are shown in section xxxxx. | ||||
Transient surge suppression must be installed on the line side of this equipment and shall be rated 480Volt (phase to ground), 480 Volt (phase to phase), suitable for over voltage category iii and shall provide protection for a rated impulse withstand voltage peak of 4kV. | ||||
UL Listed ring terminals / lugs must be used for all bus bar and grounding connections. | ||||
General Requirements | ||||
The drive provides motor overload protection in accordance with the National Electrical Code (US) | ||||
Where a motor thermistor is not fitted, or not utilised, Thermal Overload Memory Retention must be enabled by setting P11-07 = 1 | ||||
Where a motor thermistor is fitted and connected to the drive, connection must be carried out according to the information shown in section xxxx |
Routine Maintenance
The drive should be included within the scheduled maintenance program so that the installation maintains a suitable operating environment, this should include:
Ambient temperature is at or below that set out in the Environmental section, page.
Heat sink fans (where fitted) freely rotating and dust free.
The Enclosure in which the drive is installed should be free from dust and condensation; furthermore ventilation fans and air filters should be checked for correct air flow.
Checks should also be made on all electrical connections, ensuring screw terminals are correctly torqued; and that power cables have no signs of heat damage.
Product Storage
Store the drive in its original box until required. Storage and transportation of the product should be clean and dry and within the temperature range –40°C to +60°C
Installation following a period of storage
Where the drive has been stored for some time prior to installation or has remained without the main power supply present for an extended period of time, it is necessary to reform the DC capacitors within the drive according to the following table before operation. For drives which have not been connected to the main power supply for a period of more than 2 years, this requires a reduced mains voltage mains voltage to be applied for a time period, and gradually increased prior to operating the drive. The voltage levels relative to the drive rated voltage, and the time periods for which they must be applied are shown in the following table. Following completion of the procedure, the drive may be operated as normal.
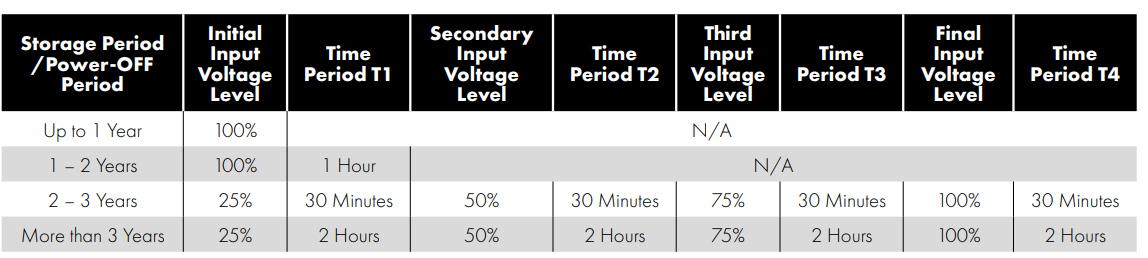
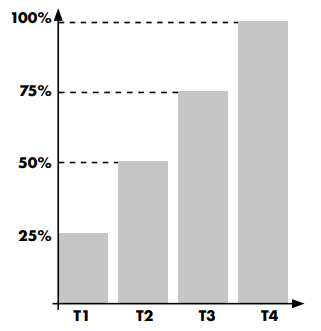
Brake resistor connections and protection
Note
The drive must be fitted with an external braking resistor (Purchased separately)
The drive has an internal brake transistor fitted as standard and is enabled automatically when the regenerative energy from the load reaches a pre-determined level as shown in the table below.
Brake resistor Activation Levels
Drive Voltage Rating | Brake transistor Turn-on Voltage | Brake transistor Turn-Off Voltage |
---|---|---|
Single and three phase 230V | 390Vdc | 378Vdc |
3 phase 400V | 780Vdc | 756Vdc |
Caution
The brake resistor must be connected between the +DC and BR Terminals of the drive as shown in the image below, failure to do so can result in damage to the drive/Brake resistor.
Danger
The voltage level at these terminals may exceed 800V DC. Stored charge may be present after disconnecting the mains power. Allow a minimum of 5 minutes discharge after power off before attempting any connection to these terminals.

Caution
The correct values must be entered into parameters P3-04 and P3-05 for the drive to protect the brake resistor against overload. this will ensure that it does not operate outside of its design limits.
To enable the built-in brake resistor overload protection follow the below steps :
Enter the resistance of the brake resistor in P3-04 (Ohms)
Enter the power of the brake resistor in P3-05 (kW)
Caution
It is highly recommended to equip the drive with a main contactor in order to provide an additional thermal overload protection for the braking resistor.
The contactor should be wired so that it will open when the resistor overheats, otherwise the drive will not be able to interrupt the main supply if the brake chopper remains closed (short-circuited) in a fault situation.
It is also recommended to wire the thermal overload protection to a digital input of the drive as an External Trip.
The diagram below shows a recommended circuit for removing mains power from the drive in the event of brake resistor overload.
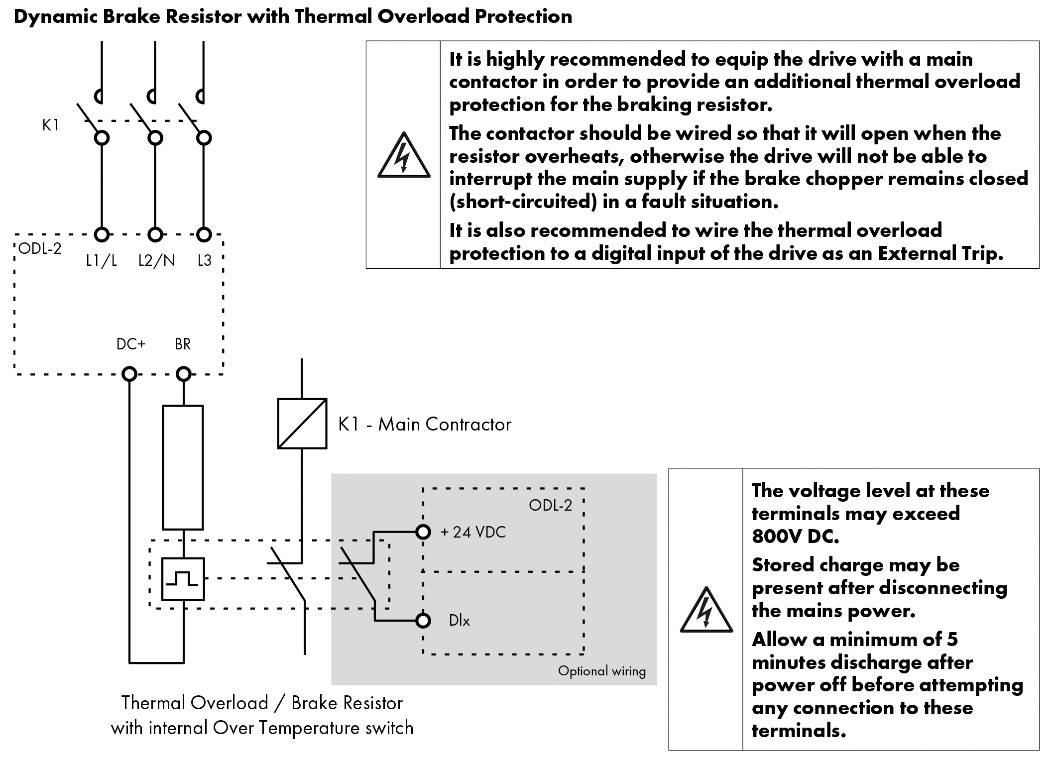
The output from the thermal overload relay/thermal switch can be wired into a digital input, that way the drive can react accordingly in the event of an overload situation.
To enable a digital input as brake resistor monitoring input follow the steps below:
Set P3-06 (Brake Resistor Temperature Monitoring Enable) to a 1 (Enabled)
Set P3-07 (Brake Resistor Temperature Monitoring trip reaction) to the required reaction as per the table below.
Setting | Function |
---|---|
0 | Normal Stop, Trip (Ot-Br) After stopping. |
1 | Immediate Trip (Ot-Br), Apply motor Brake |
2 | Warning Only No Trip. (Show the trip (Ot-Br) on the display as an intermittent status message) |
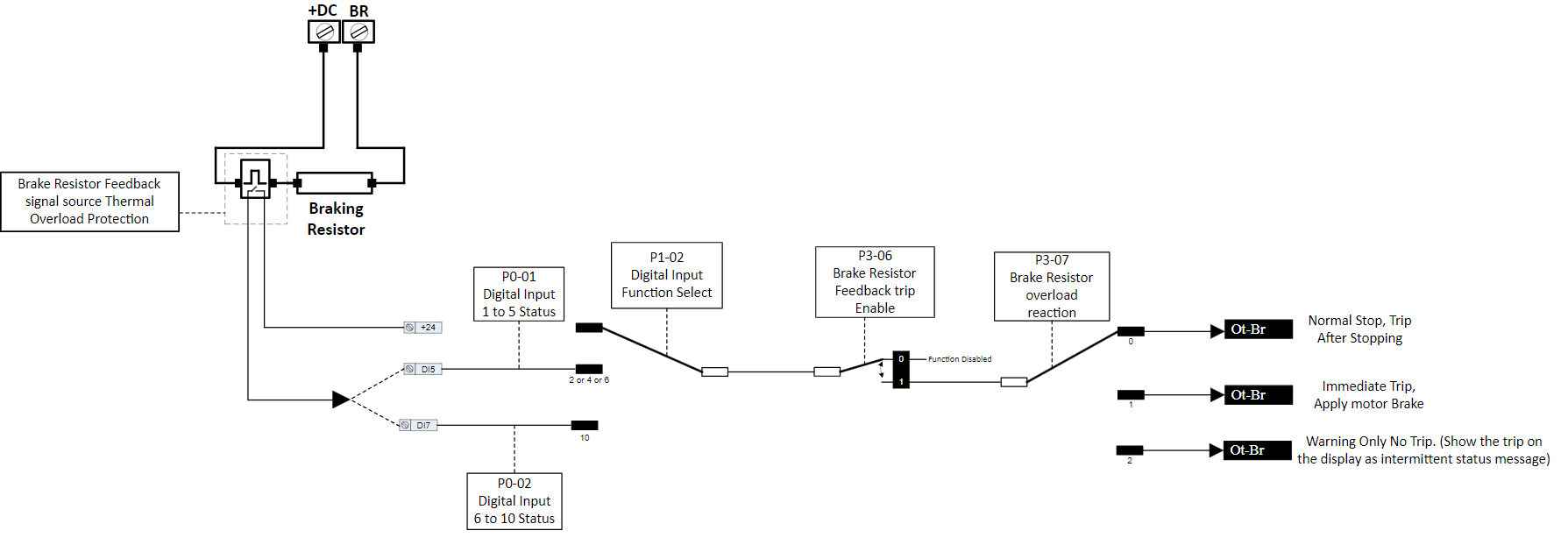
Important
The Resistor power ratings shown are guideline only, the values should be calculated based on the individual application, considering the braking power and duty cycle of the elevator.
The resistance of the braking resistor must not be less than the minimum values shown in the table below.
Model Code | Recommended Brake Resistance (Minimum) | Resistor power rating (W) |
---|---|---|
ODL-3-220105-142SB_ | 35 (20) | 1000 |
ODL-3-220180-342SB_ | 20 (20) | 1000 |
ODL-3-220240-342SB_ | 20 (20) | 1500 |
ODL-3-320300-342SB_ | 20 (12) | 2000 |
ODL-3-240095-342SB_ | 100 (40) | 1000 |
ODL-3-240140-342SB_ | 75 (40) | 1500 |
ODL-3-340180-342SB_ | 50 (22) | 2000 |
ODL-3-340240-342SB_ | 40 (22) | 3000 |
ODL-3-340300-342SB_ | 50 (22) | 4000 |